Hydroponic food growth complete modular system.
Design, development and prototype of a large scale modular hydroponic food growing system, a highly regulated 'clean room' environment enabling 24/7 365 day growth cycles of small salad leaves and similar to maximise potential and remove risk/failure. The full cycle creates a zero human touch and 'ready to eat' product through a fully automated seeding, growth, harvesting and packaging environment.
Full project management of the design process from initial concept ideation to prototype procurement and fabrication.
User centred research and design thinking; Existing product audit; market evaluation;
Concept design; Concept models; Test rig prototypes; Ergonomic assessment; DfMA
SolidWorks CAD full assembly model (1000+ part assembly); mechanical design; mechanism proving, test rig fabrication and test. Pultruded section framework design; integration of HVAC services and considerations for plant; Sheet metal design; CFD (internal and external commission). Design and prototype proprietary fluids/waste and power connections.
User centred research and design thinking; Existing product audit; market evaluation;
Concept design; Concept models; Test rig prototypes; Ergonomic assessment; DfMA
SolidWorks CAD full assembly model (1000+ part assembly); mechanical design; mechanism proving, test rig fabrication and test. Pultruded section framework design; integration of HVAC services and considerations for plant; Sheet metal design; CFD (internal and external commission). Design and prototype proprietary fluids/waste and power connections.
Digital data sets for development to pre-production prototype procurement/RFQ.
Evolution through the design process of a 13.7m ‘clean room’ with considerations for standards and regulatory control, provision for power, fluids, C02, airflow, temperature, humidity and waste plus LED lighting panels. Further design criteria for evacuation and harvesting, cleaning, seeding and filling. Also for 'clean and dirty' areas including rear plant modules and rear access for maintenance.
Design and fabrication of prototype modular growth cradles utilising rapid technologies, pultruded sections and 3D printed components including fabrication of stainless steel growing trays and mesh growth supports.
Phase 1 site layout for 72 units providing 6500 m2 of growing footprint.
Design and procurement of a 4m prototype growing room fabricated from cold rolled steel, clad and sealed for up to 10 cradle units including prototype stainless steel air ducts and rear service module for site installation to enable real world growth test and evaluation.
Virtual assessment via CFD for water flow efficiency and pipe diameter sizing and air flow through the side plenums and across the growth areas from intake to exhaust to address even distribution of C02 and nutrients.
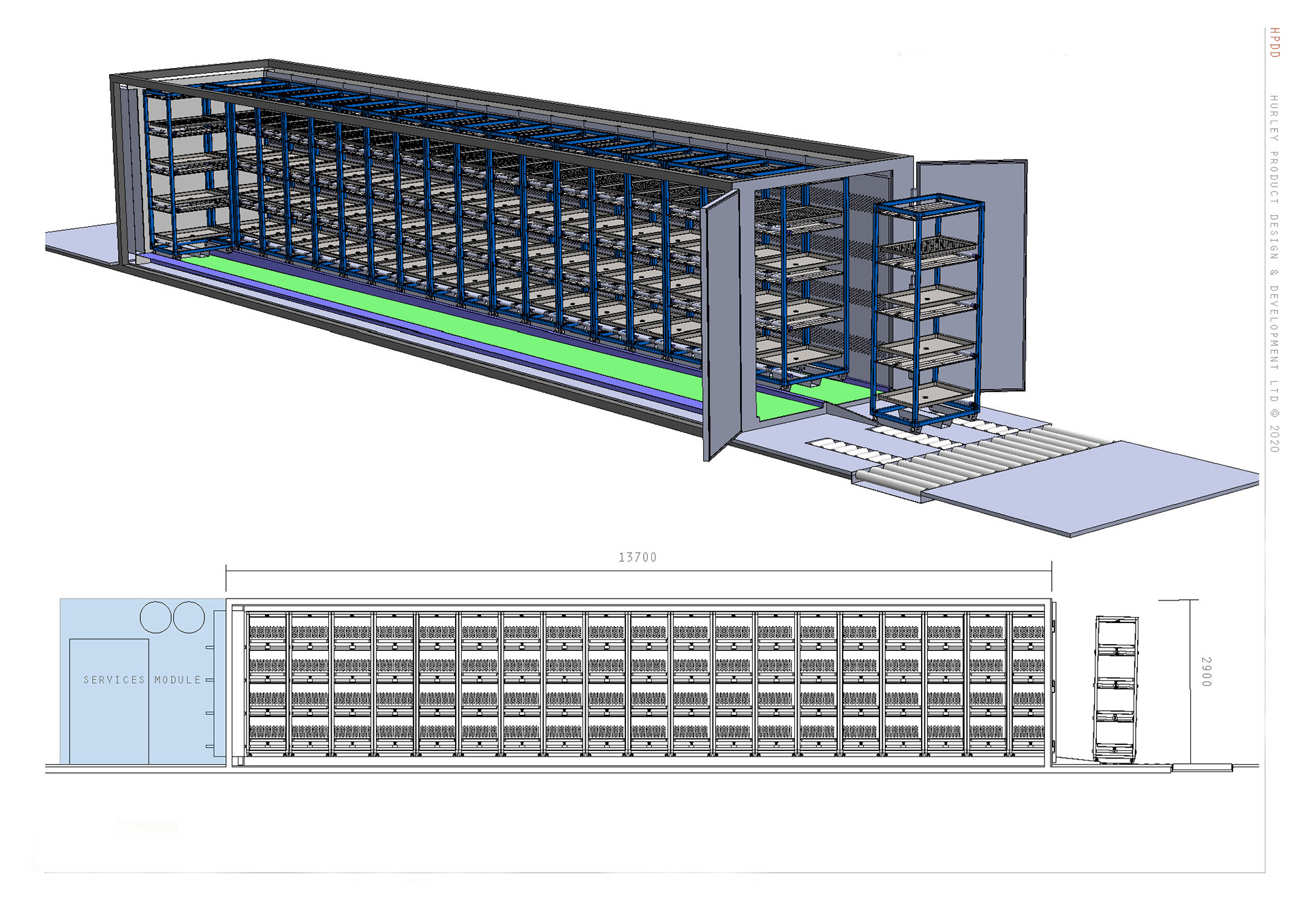
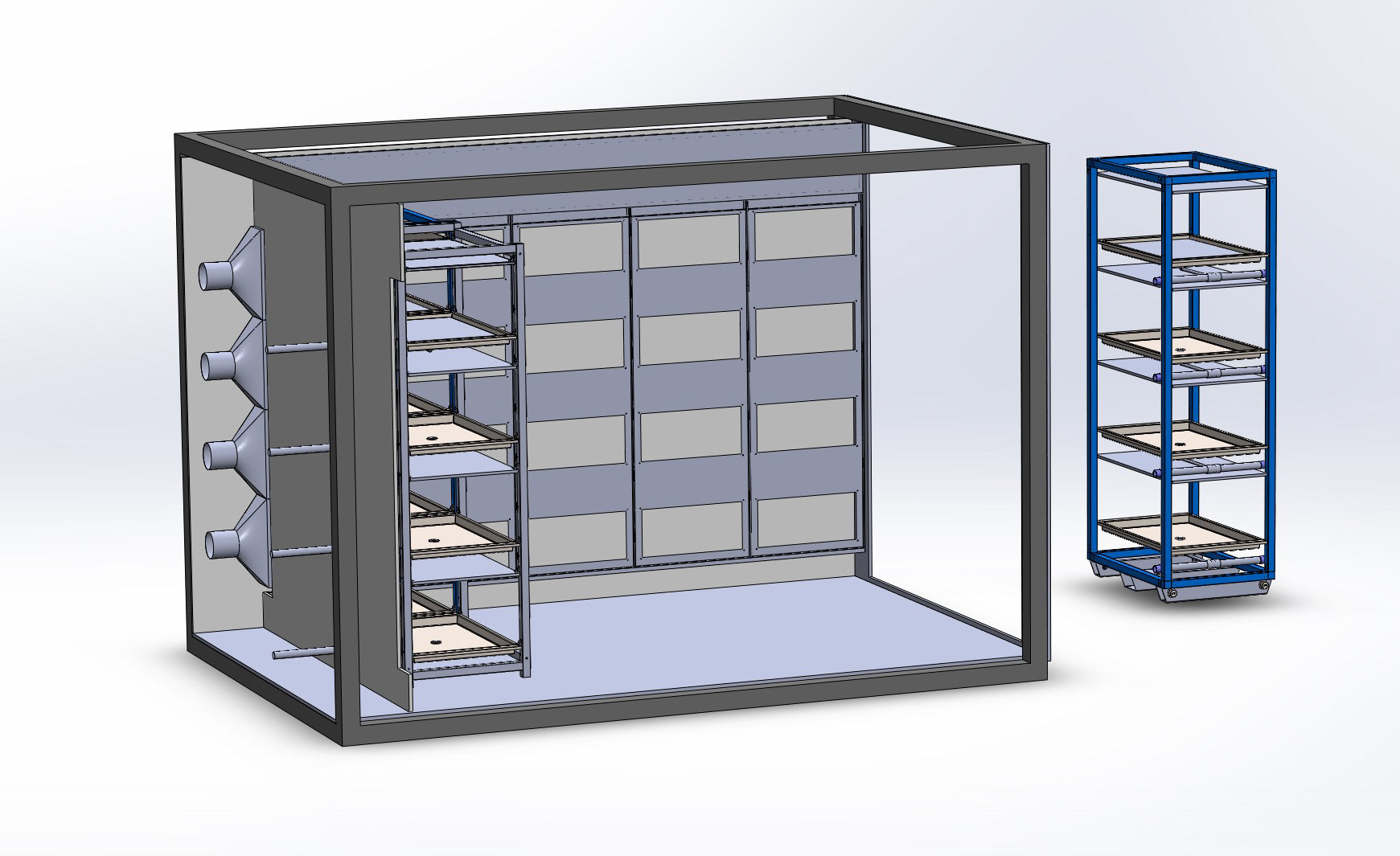
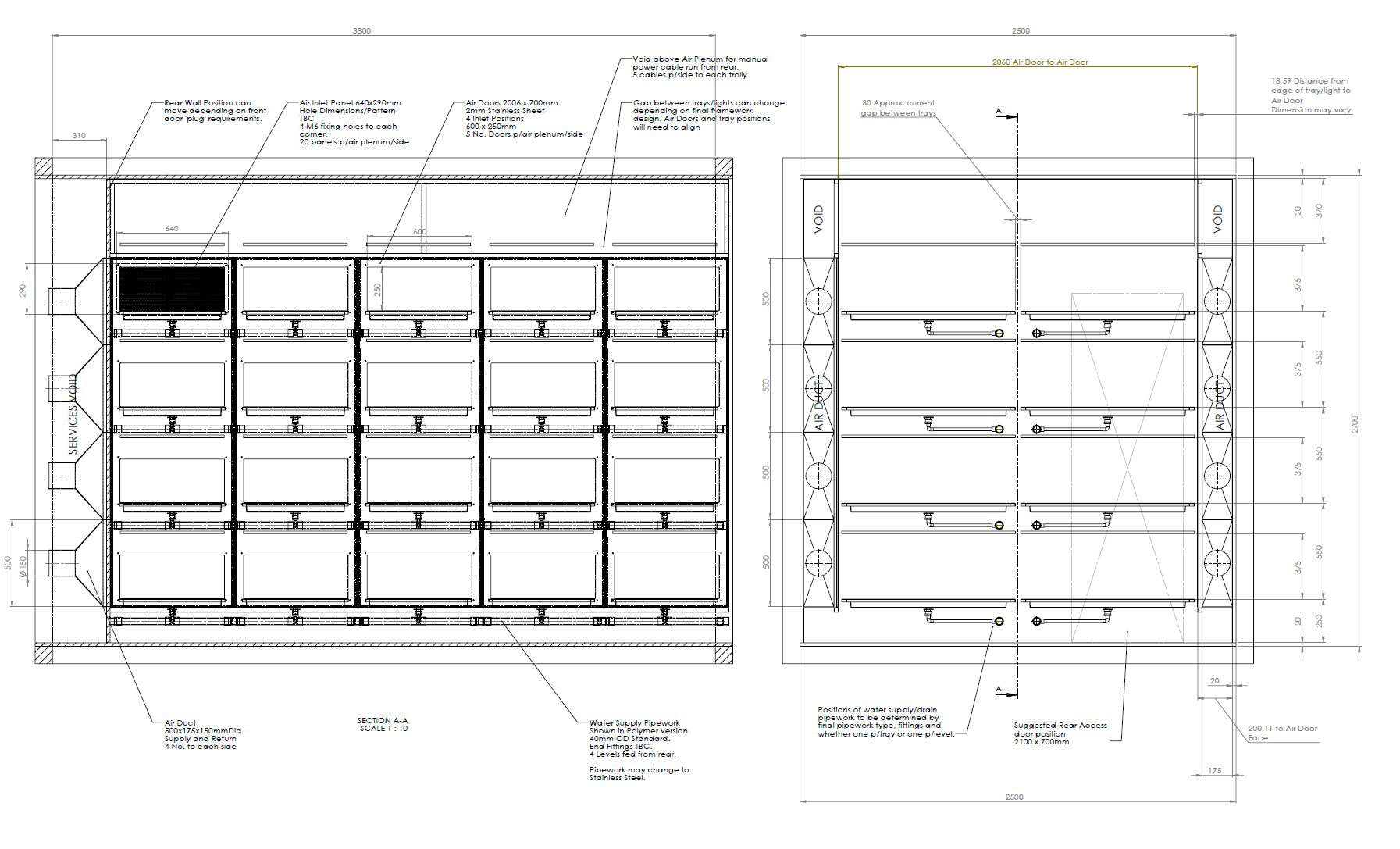
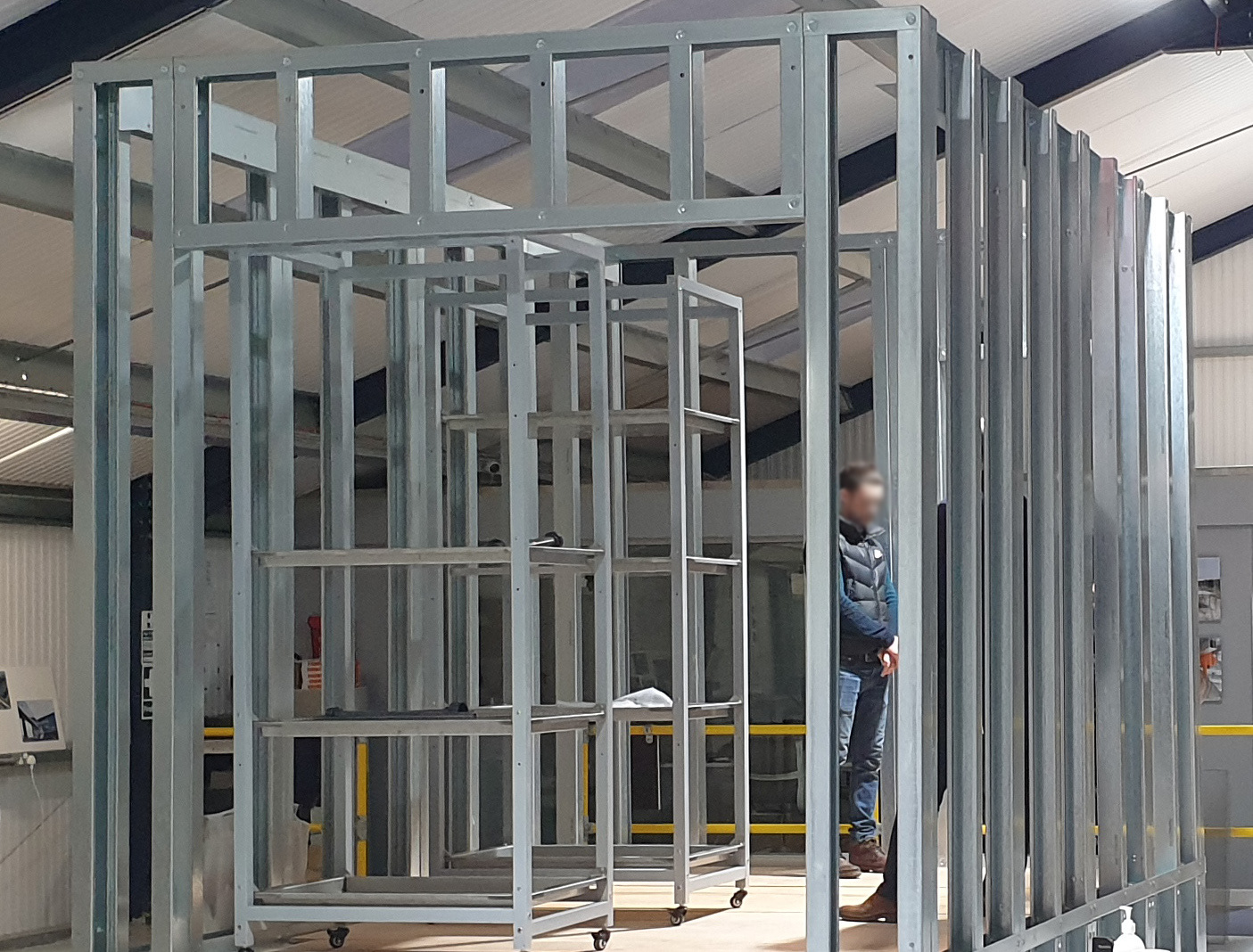
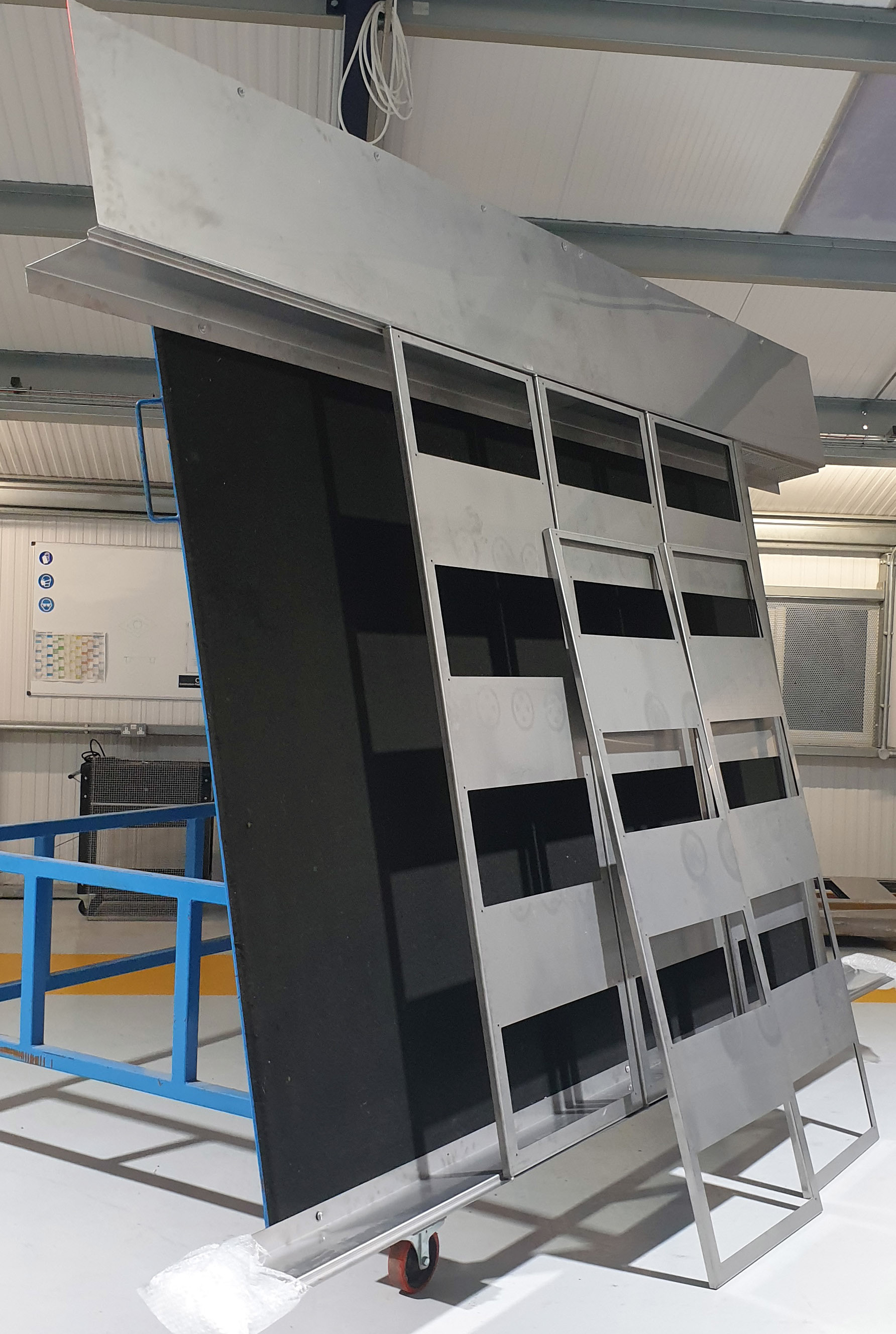
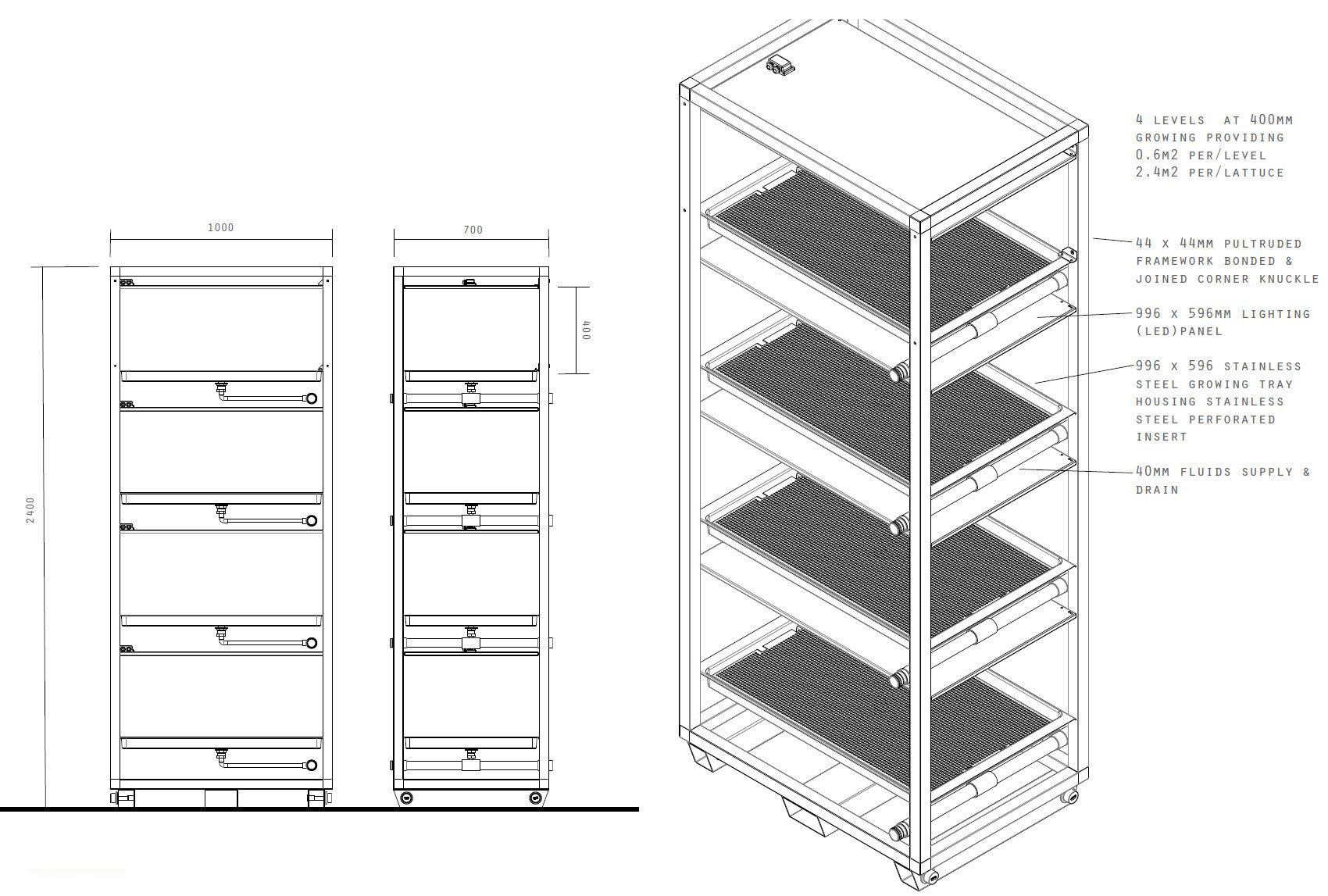
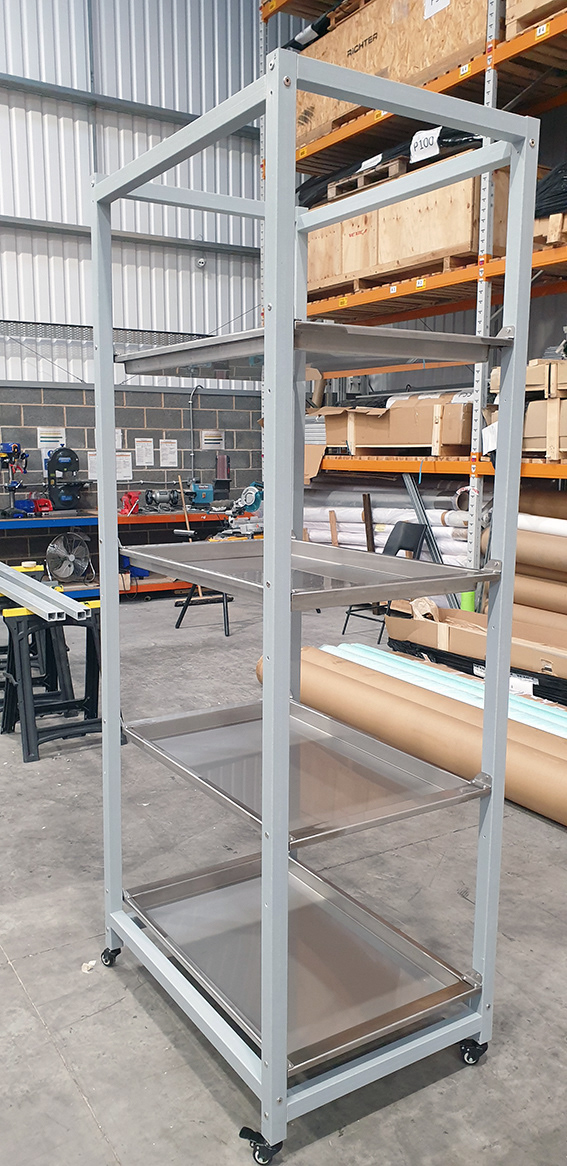
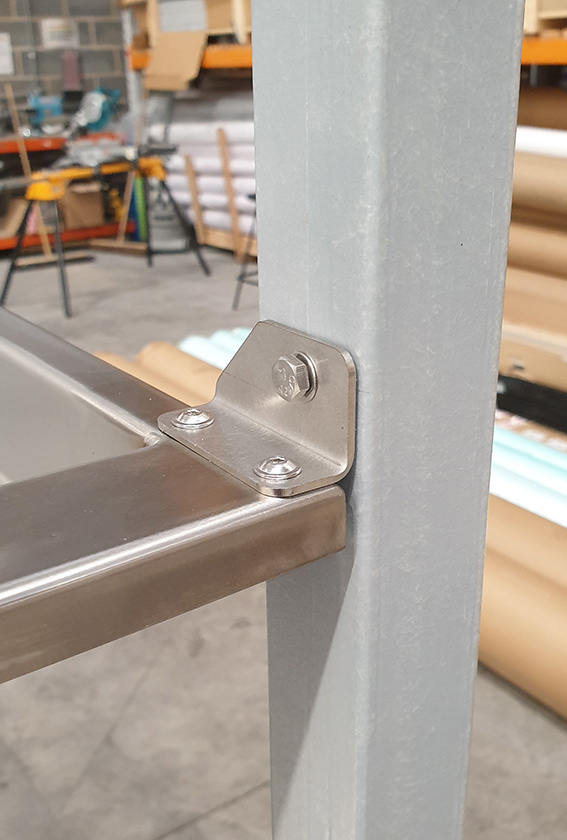
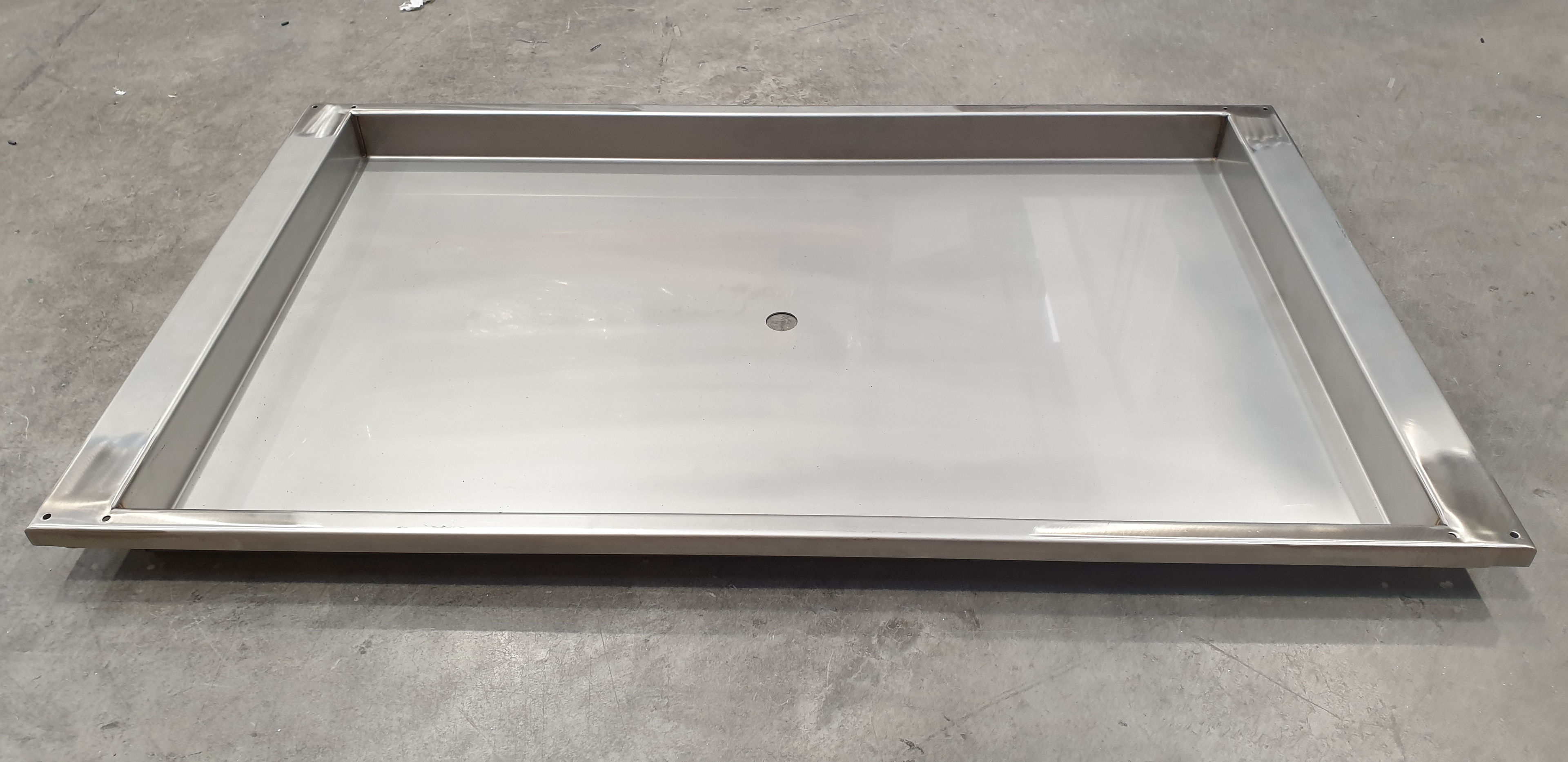
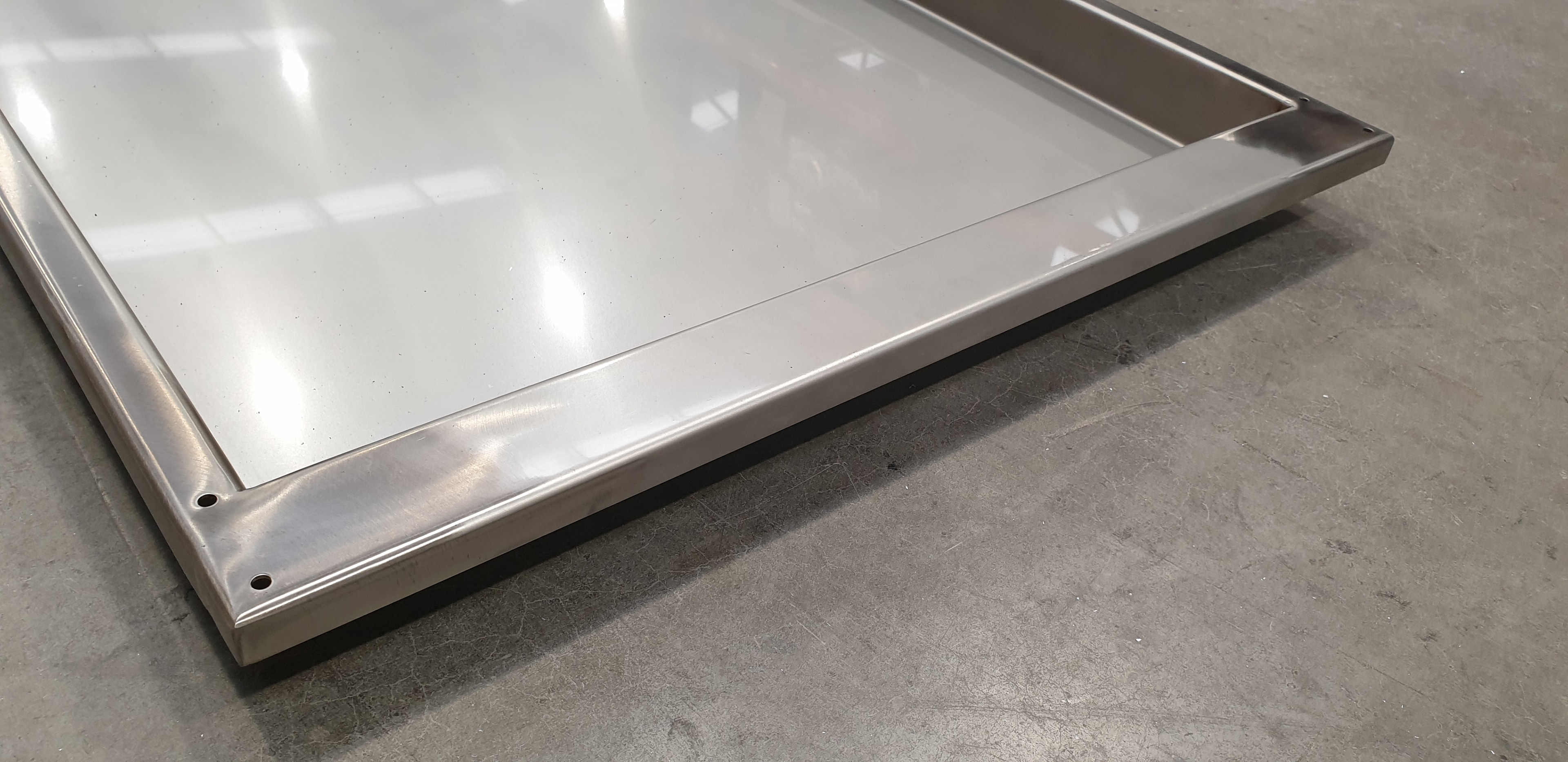
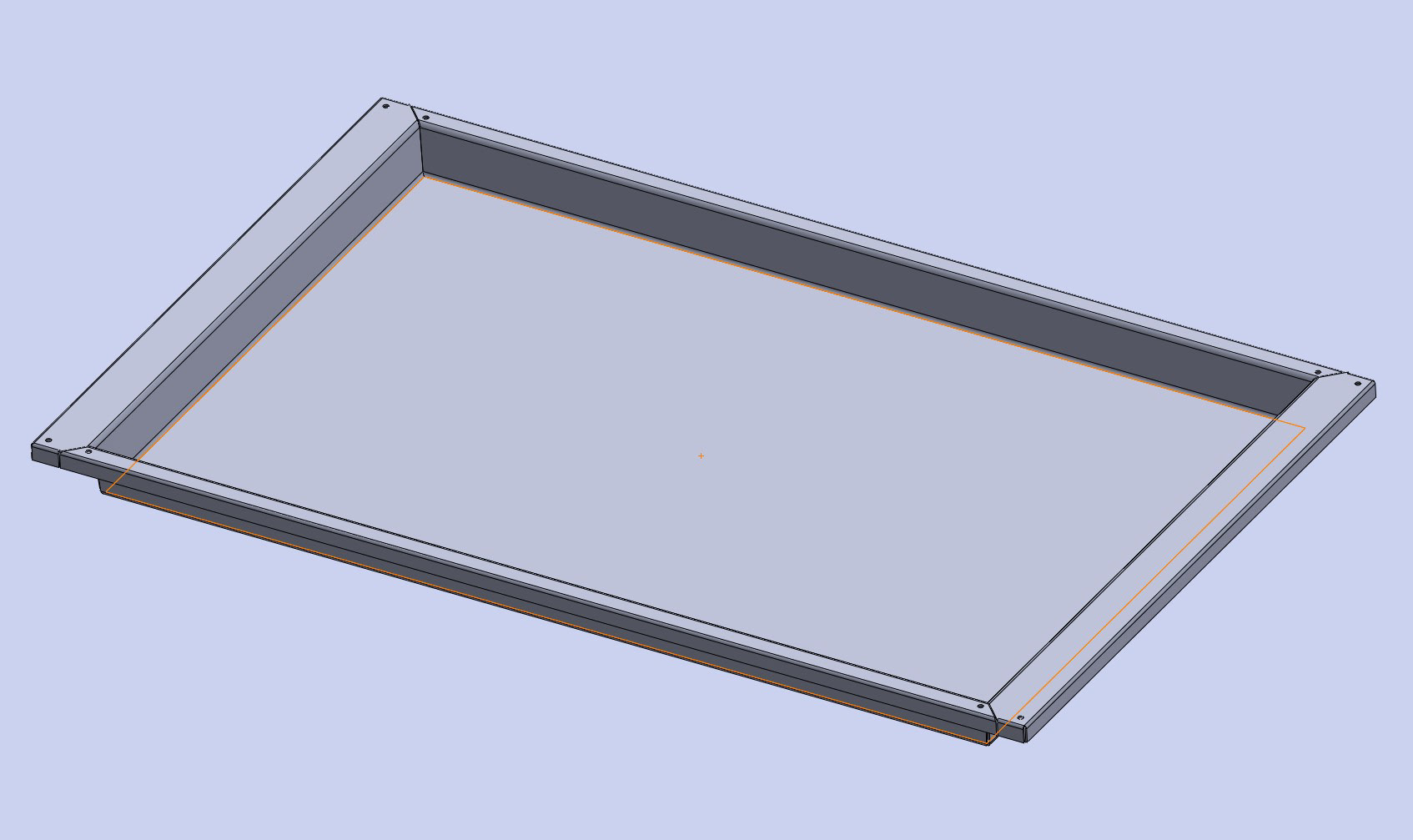
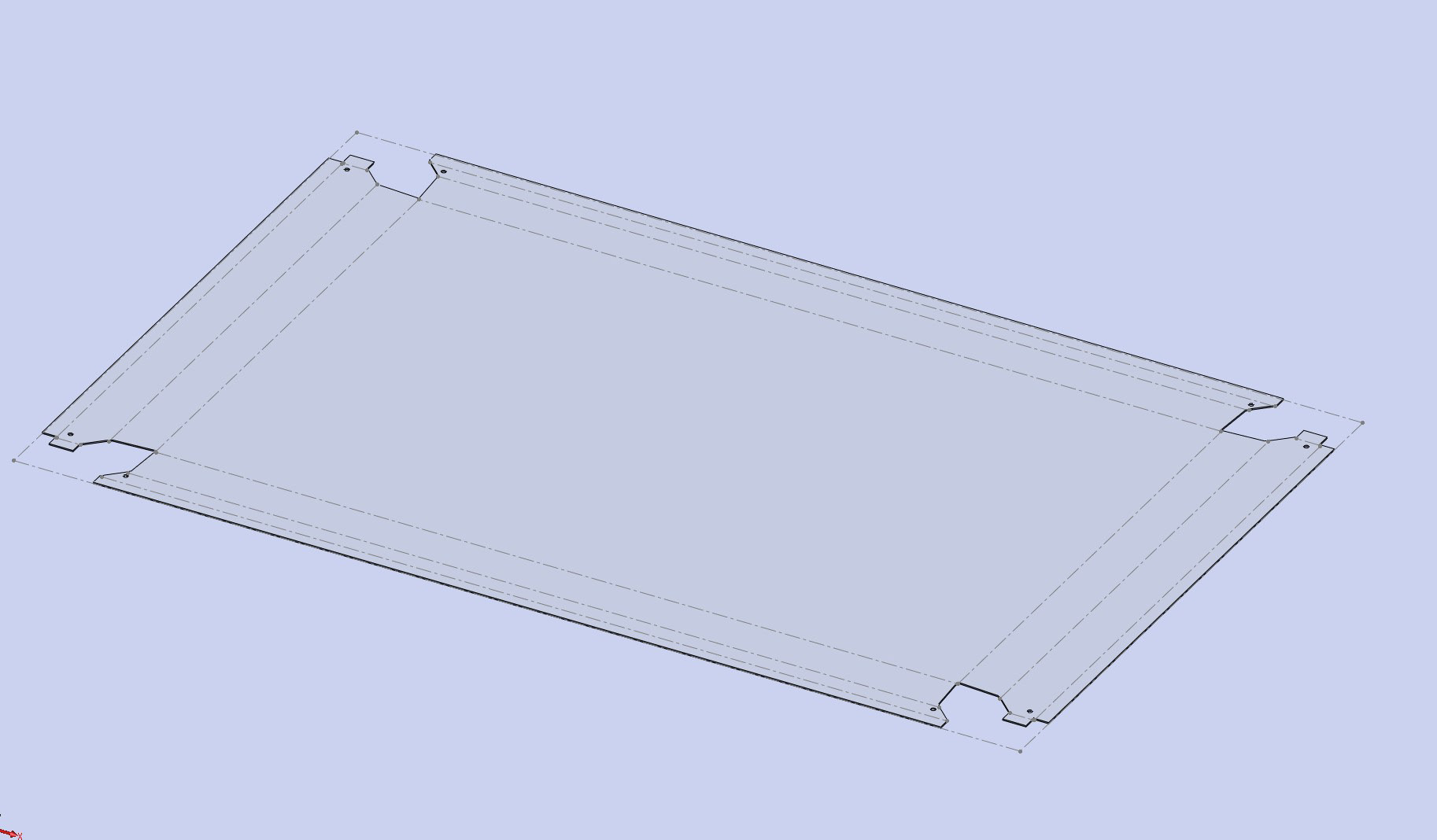
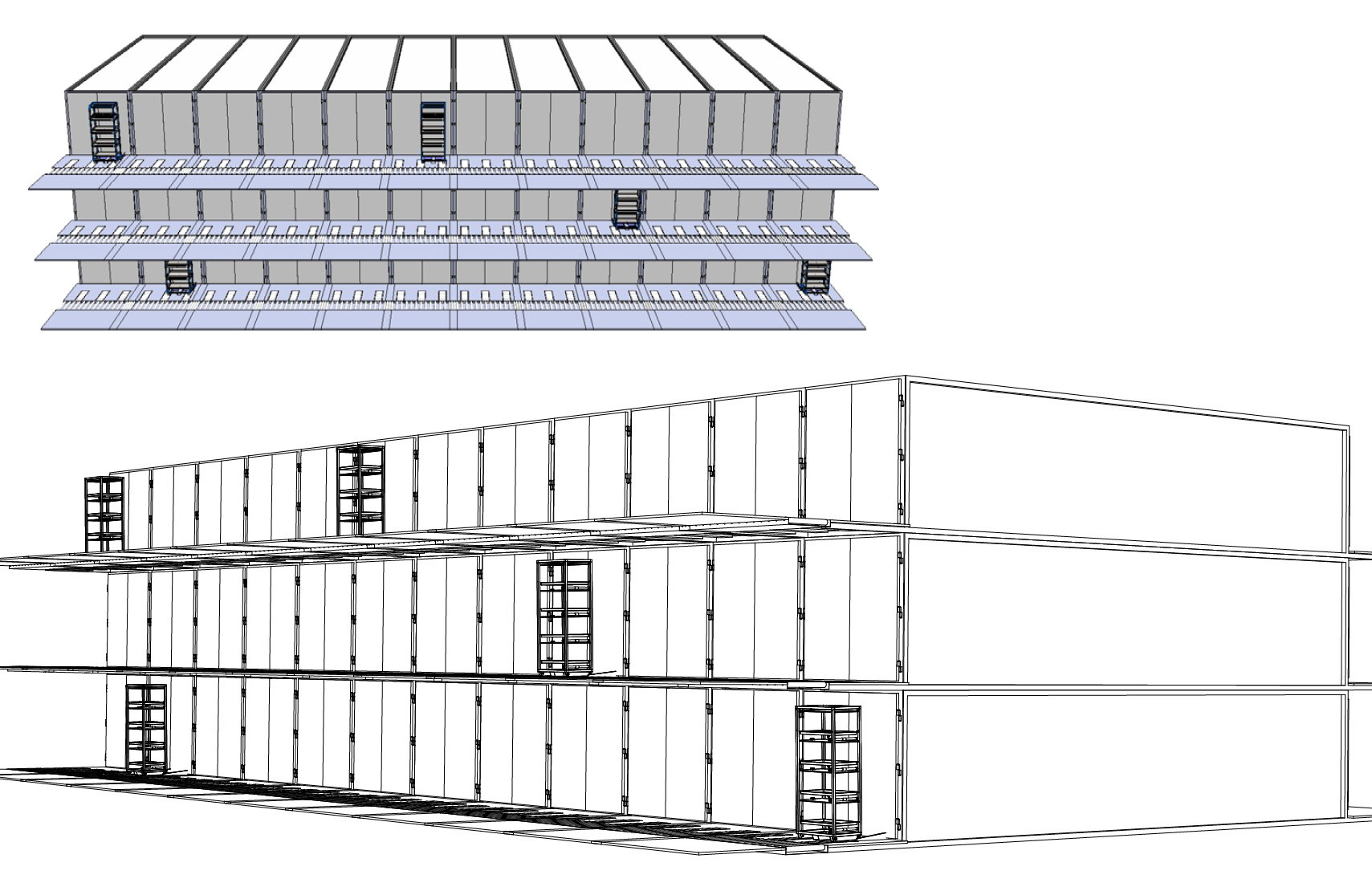
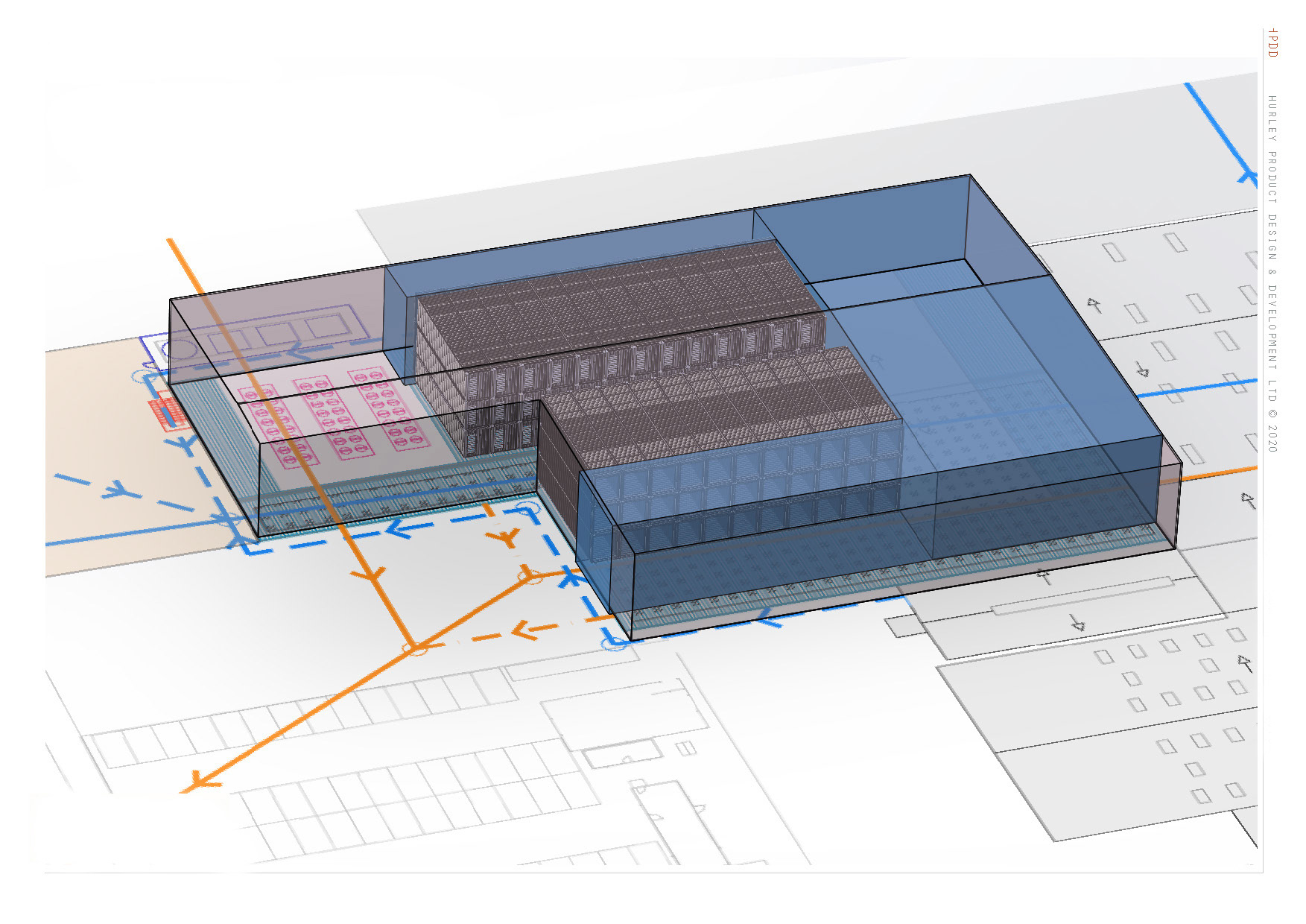
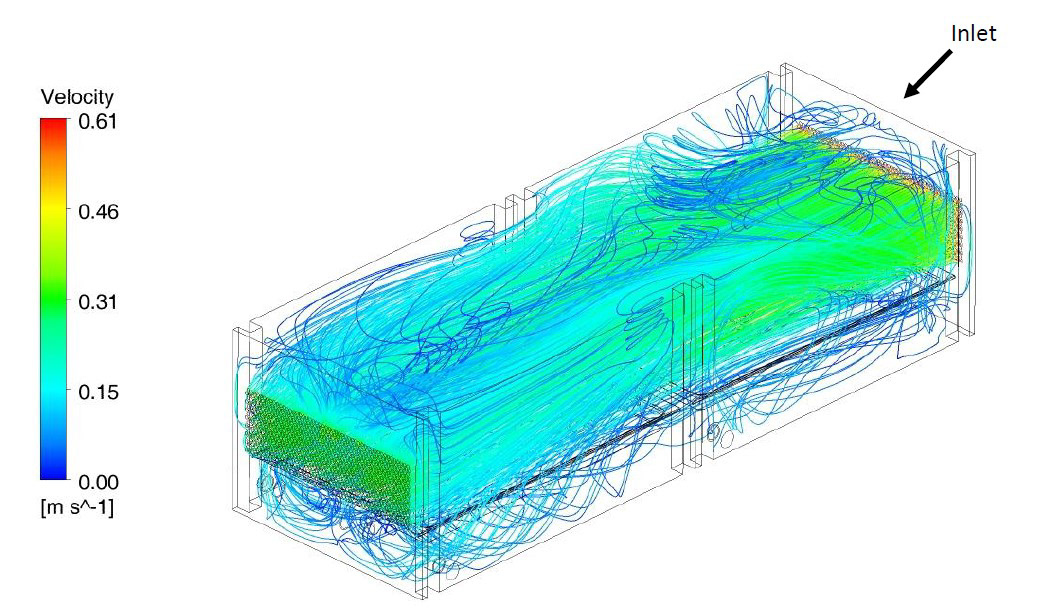