C3 Headsets - TC-200 Call Centre Headset
Clement Clarke Communications Plc
User Centred Research; Behavioural Research; Existing Product Audit; Competitor Analysis; Concept Design; Concept Models; Ergonomic Assessment: Electronics Integration; Test Rig Prototypes; Pre-Production Prototypes; Design For Manufacture; Engagement with the Production Process; Presentation at Launch
SolidWorks CAD full assembly model production engineered for mass production injection moulding tooling.
Materials: Hostaform C9021 Acetal Copolymer; Kreiburg K Thermoplastic Elastomer.
SolidWorks CAD full assembly model production engineered for mass production injection moulding tooling.
Materials: Hostaform C9021 Acetal Copolymer; Kreiburg K Thermoplastic Elastomer.
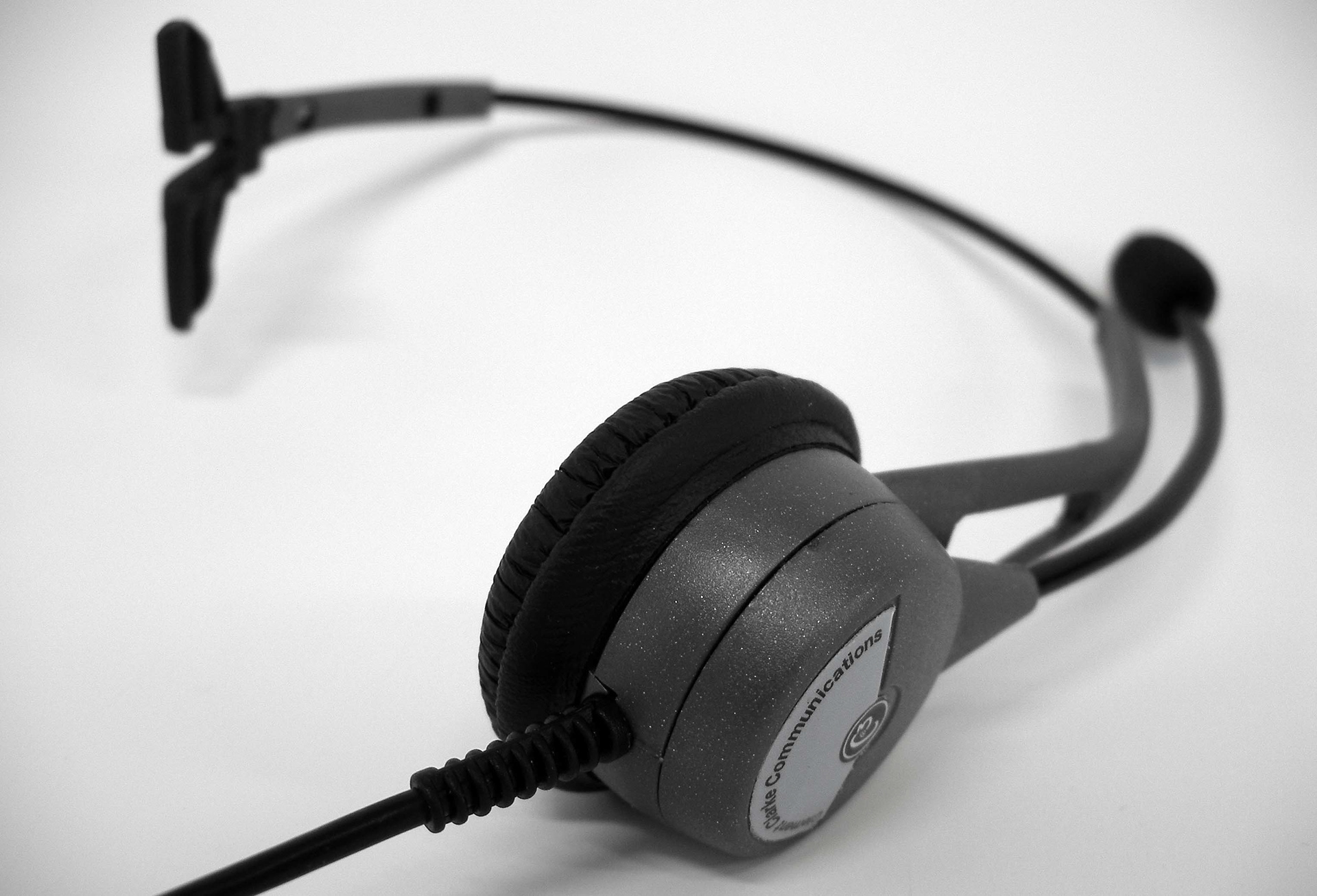
A nine month project from blank page to launch, the TC-200 reshaped C3 Headsets' product offer to a comfortable lightweight headset with a number of unique functions - a soft flexible split 'fish tail' rest that removed pressures to the side of the head via a two-shot over moulding, microphone boom positioner knibs for both left and right handed use moulded into the plastics and an easy to clean construction for hot desk environments.
A reduction by over one third for the production cost of TC-200 over C3 Headsets' previous model - TC-1 achieved primarily by a reduction in the number of components and specifically, a snap construction of the three main body housings made possible by a collapsible core tool (see below images). This improved strength, still enabled rotation for the boom and reduced assembly time significantly via a 'tool-free' greatly simplified assembly process.
A reduction by over one third for the production cost of TC-200 over C3 Headsets' previous model - TC-1 achieved primarily by a reduction in the number of components and specifically, a snap construction of the three main body housings made possible by a collapsible core tool (see below images). This improved strength, still enabled rotation for the boom and reduced assembly time significantly via a 'tool-free' greatly simplified assembly process.
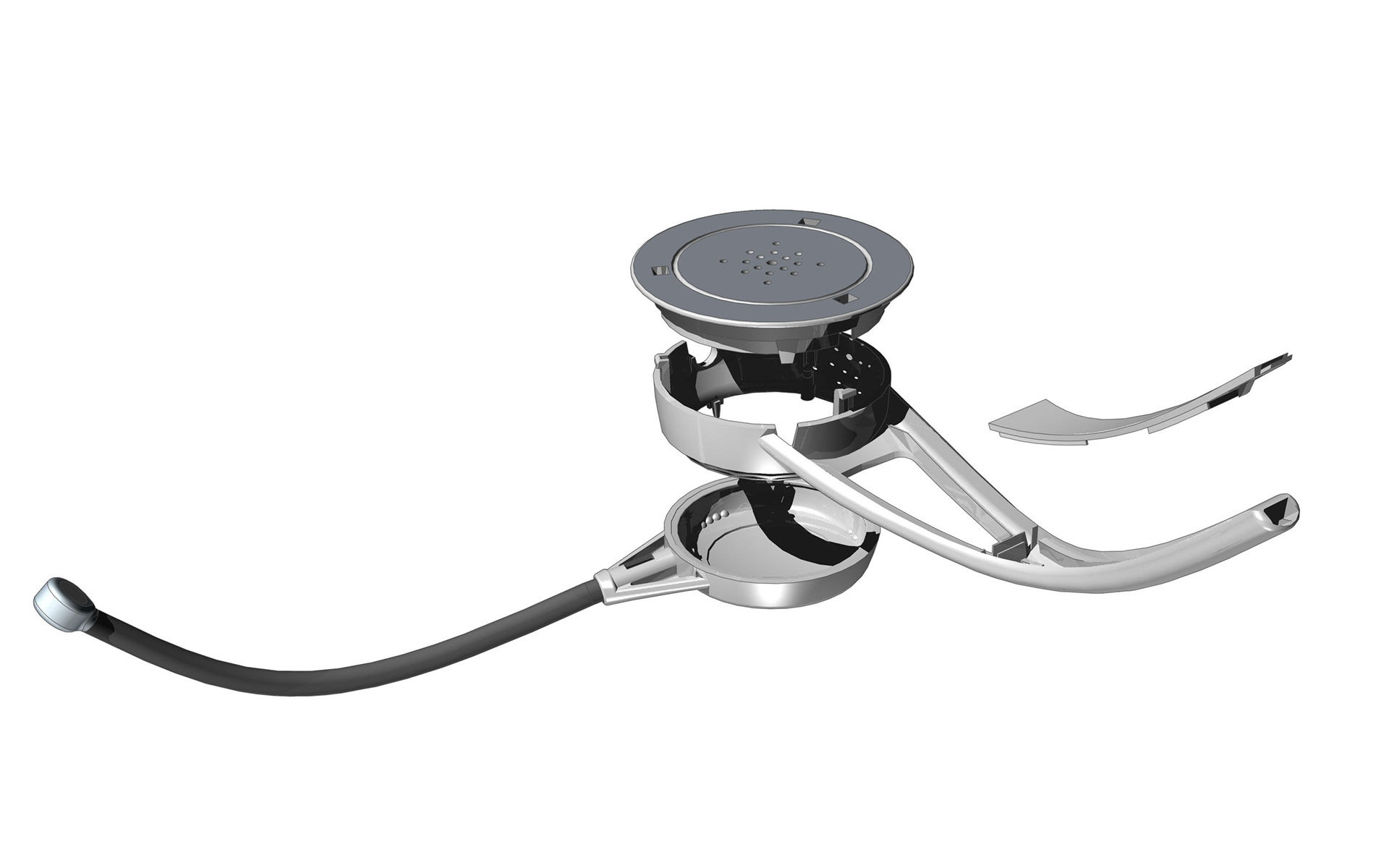
A combination of specifically placed 'C' channels in the split arm and material selection (acetal copolymer - an engineering polymer with elastomer memory) allowed subtle movements for ergonomic variation, providing adjustability for the end user - with the cover panel over the adjustment cavity for the sleeved spring steel headband welded ultrasonically.
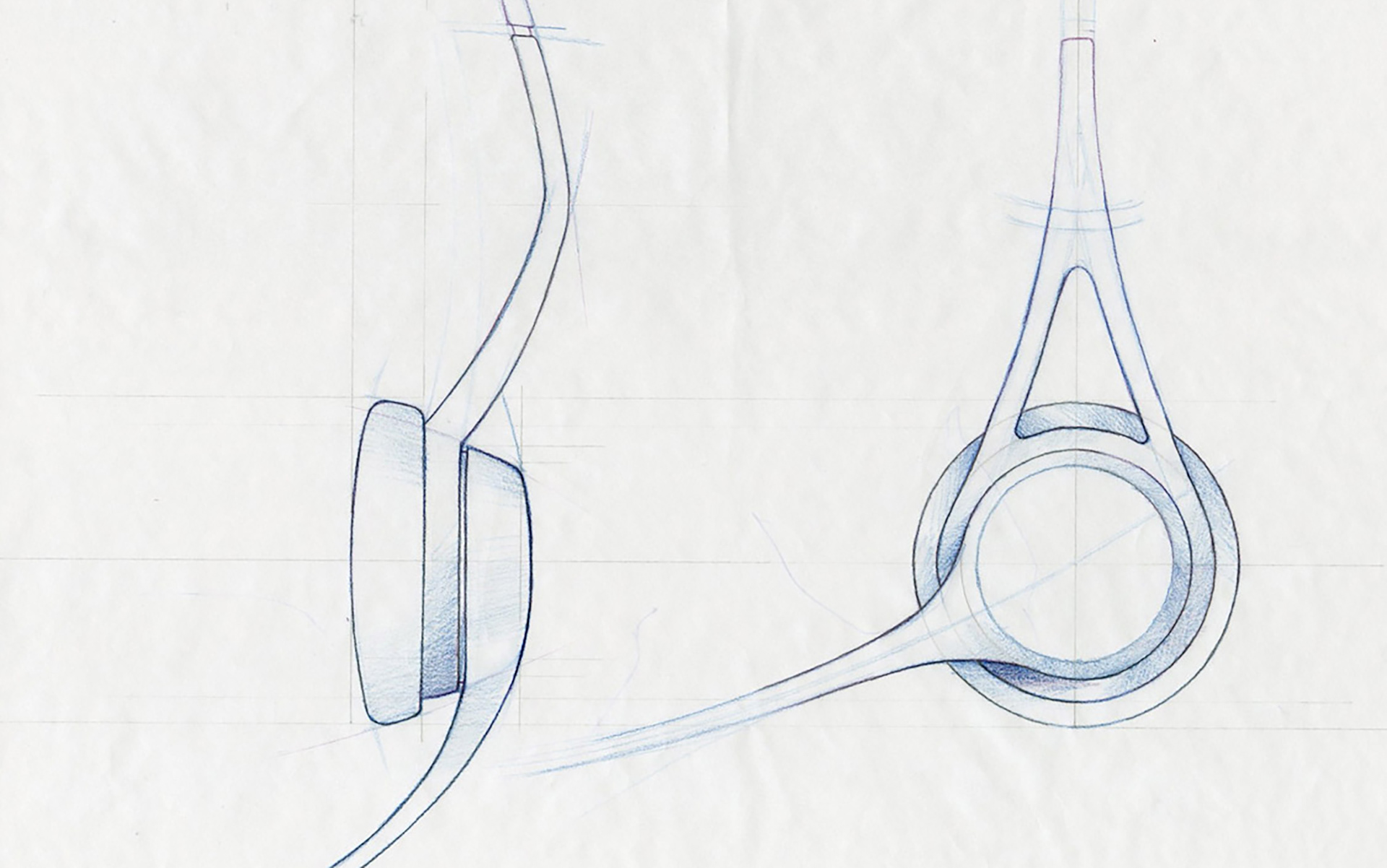
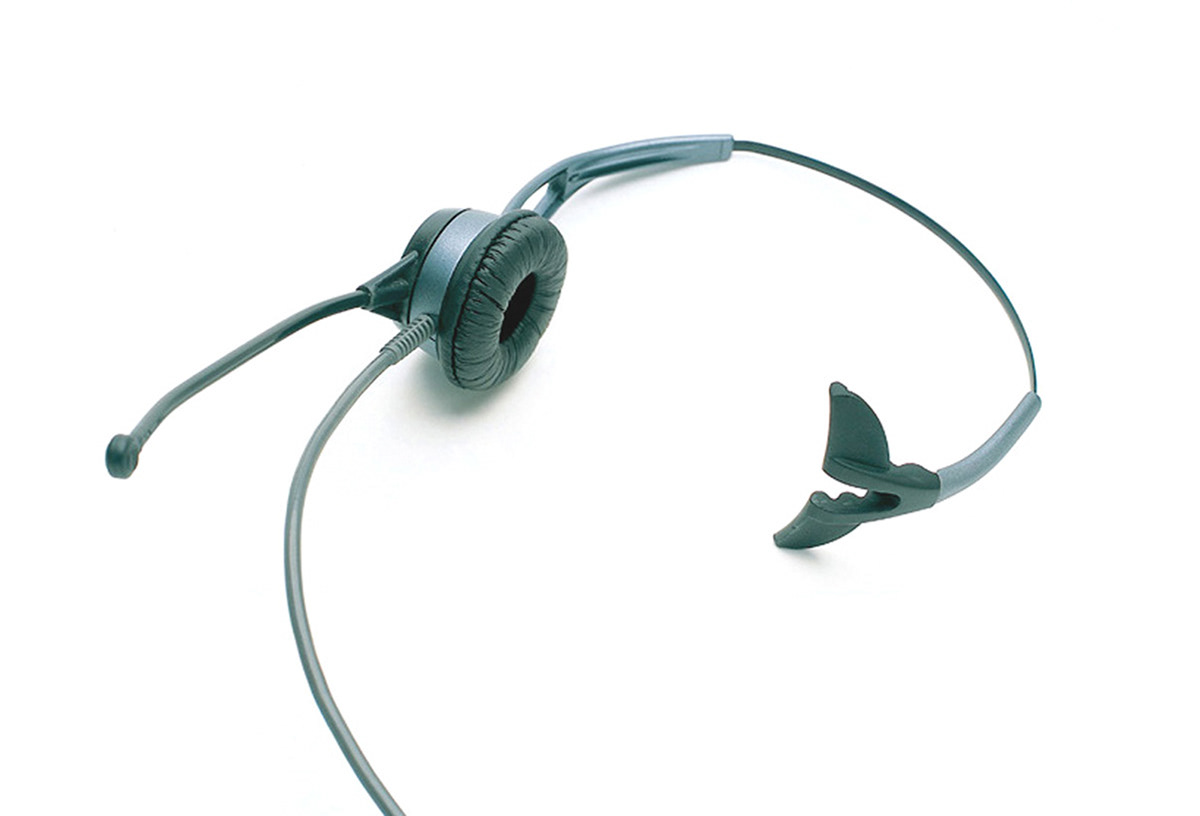
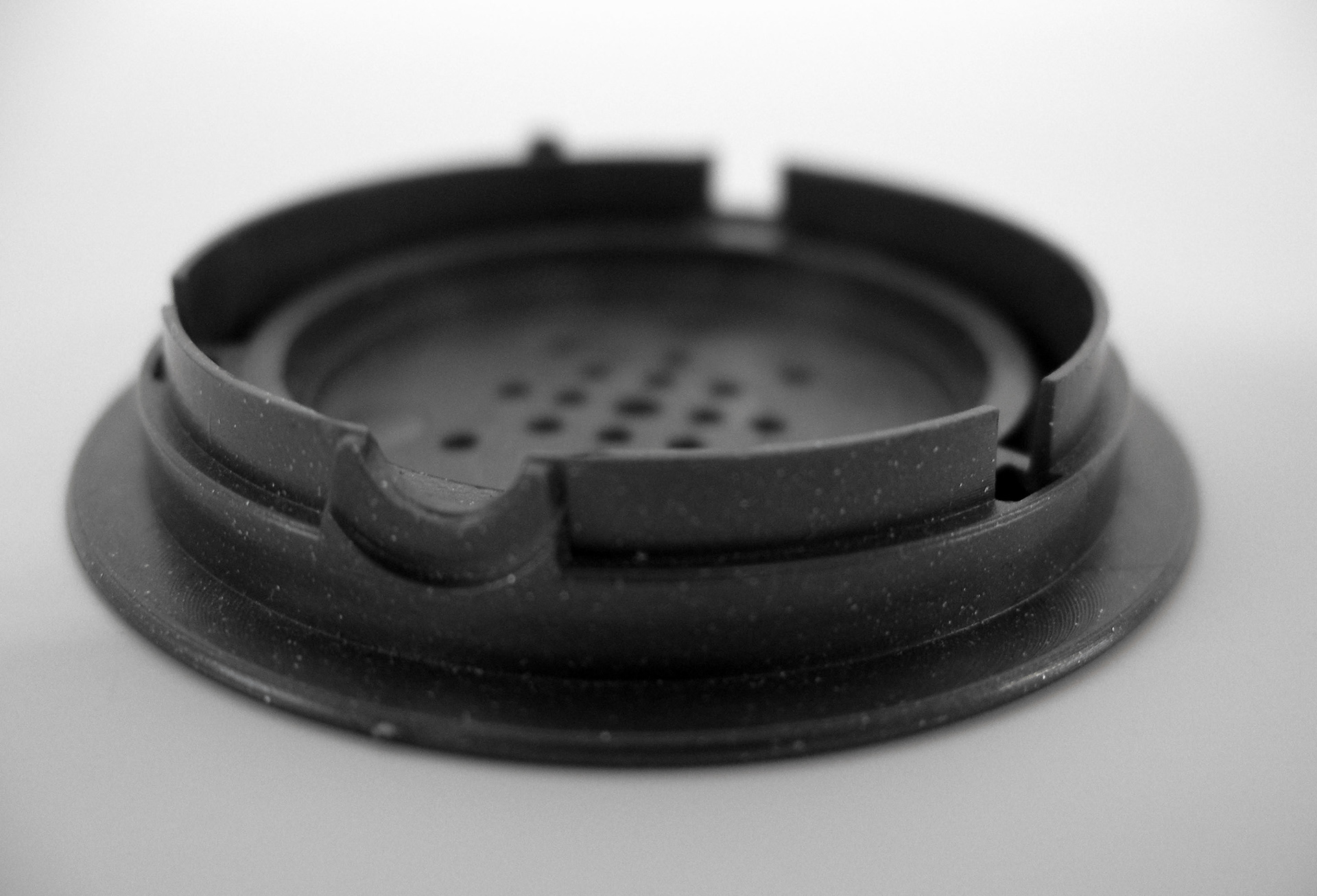
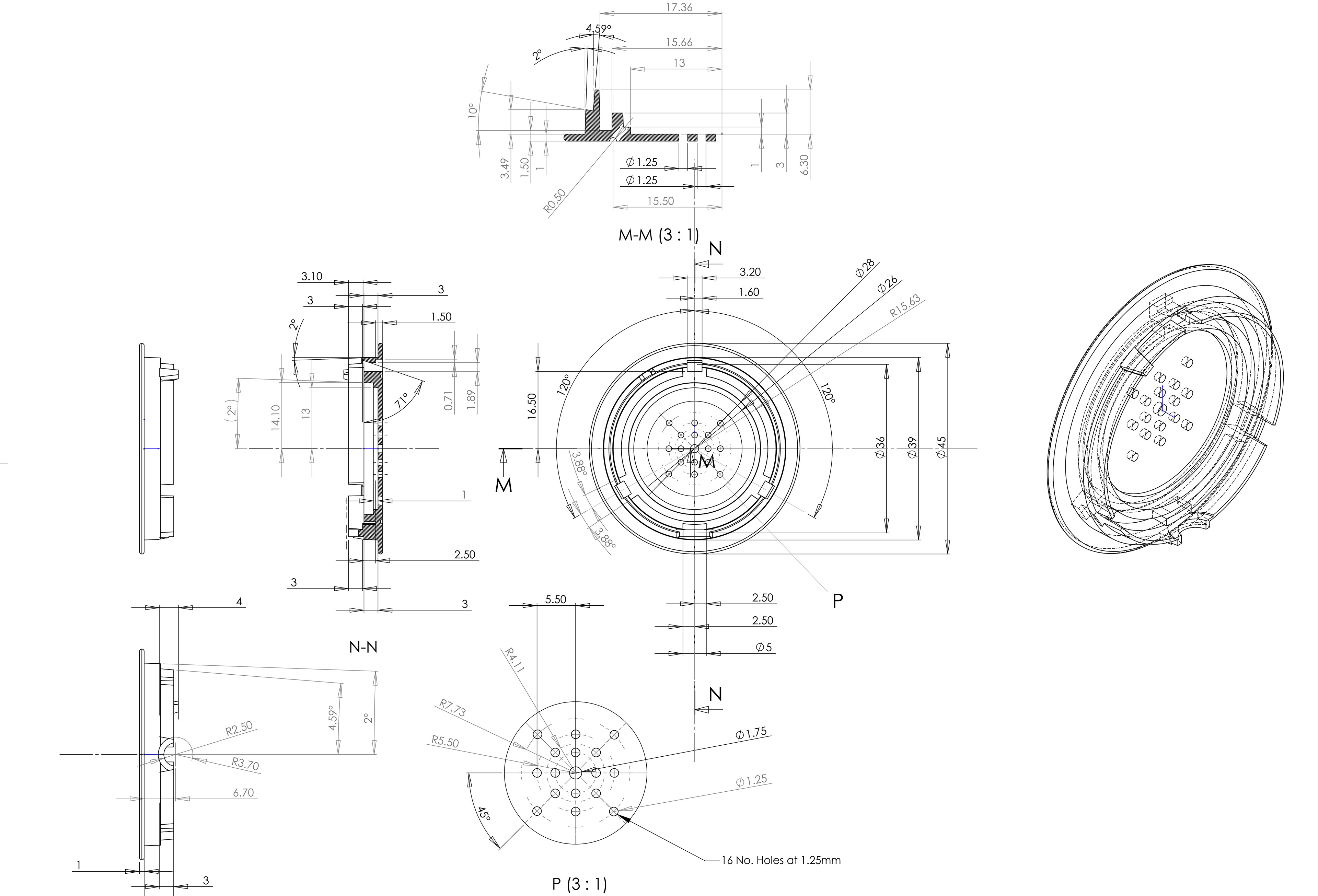
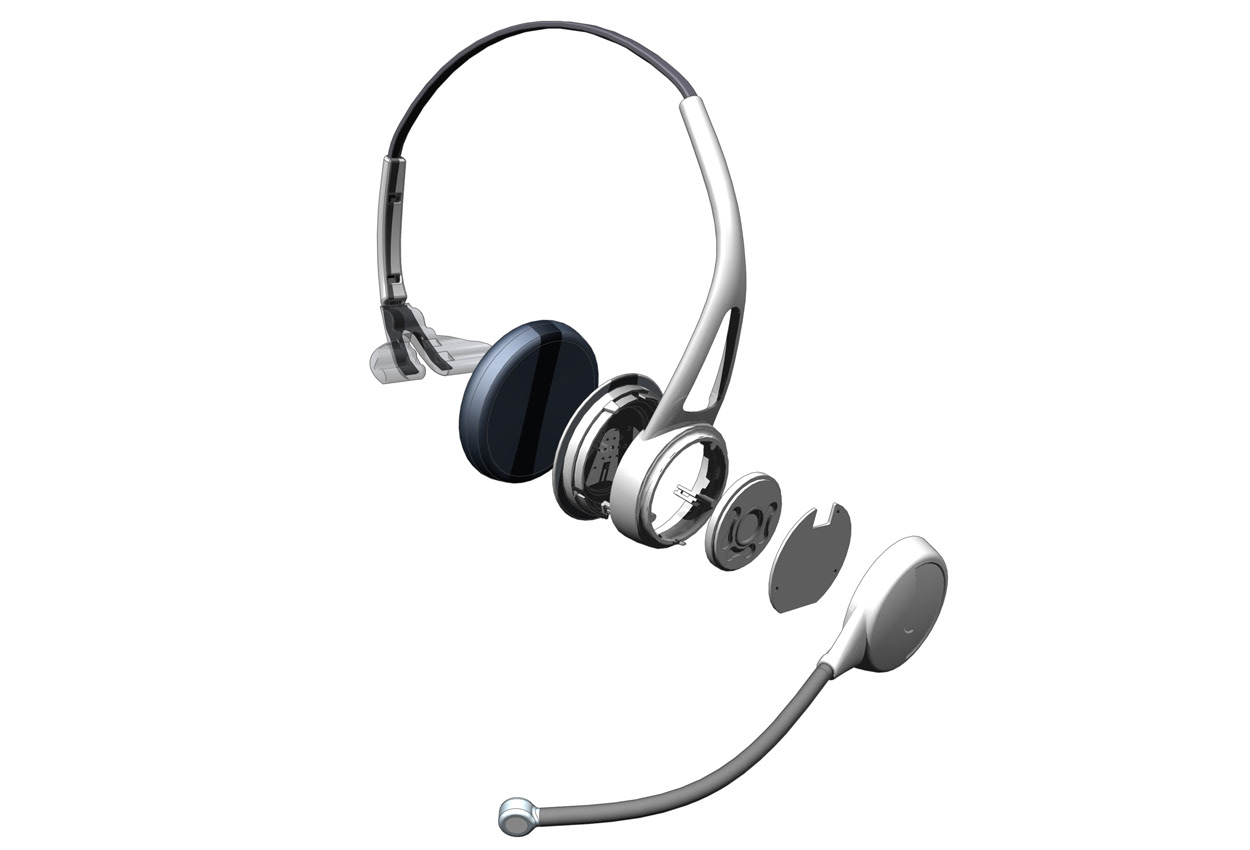
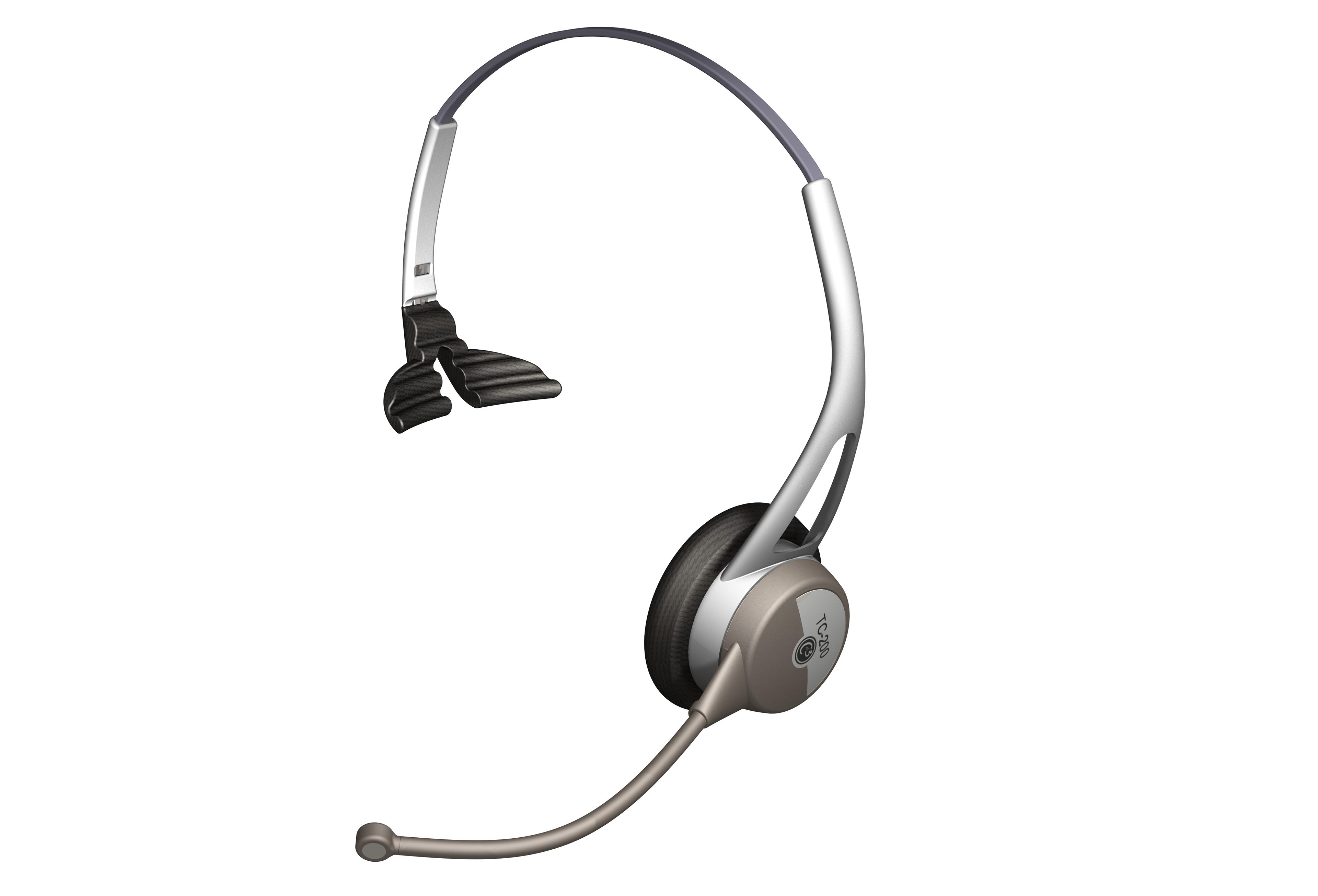
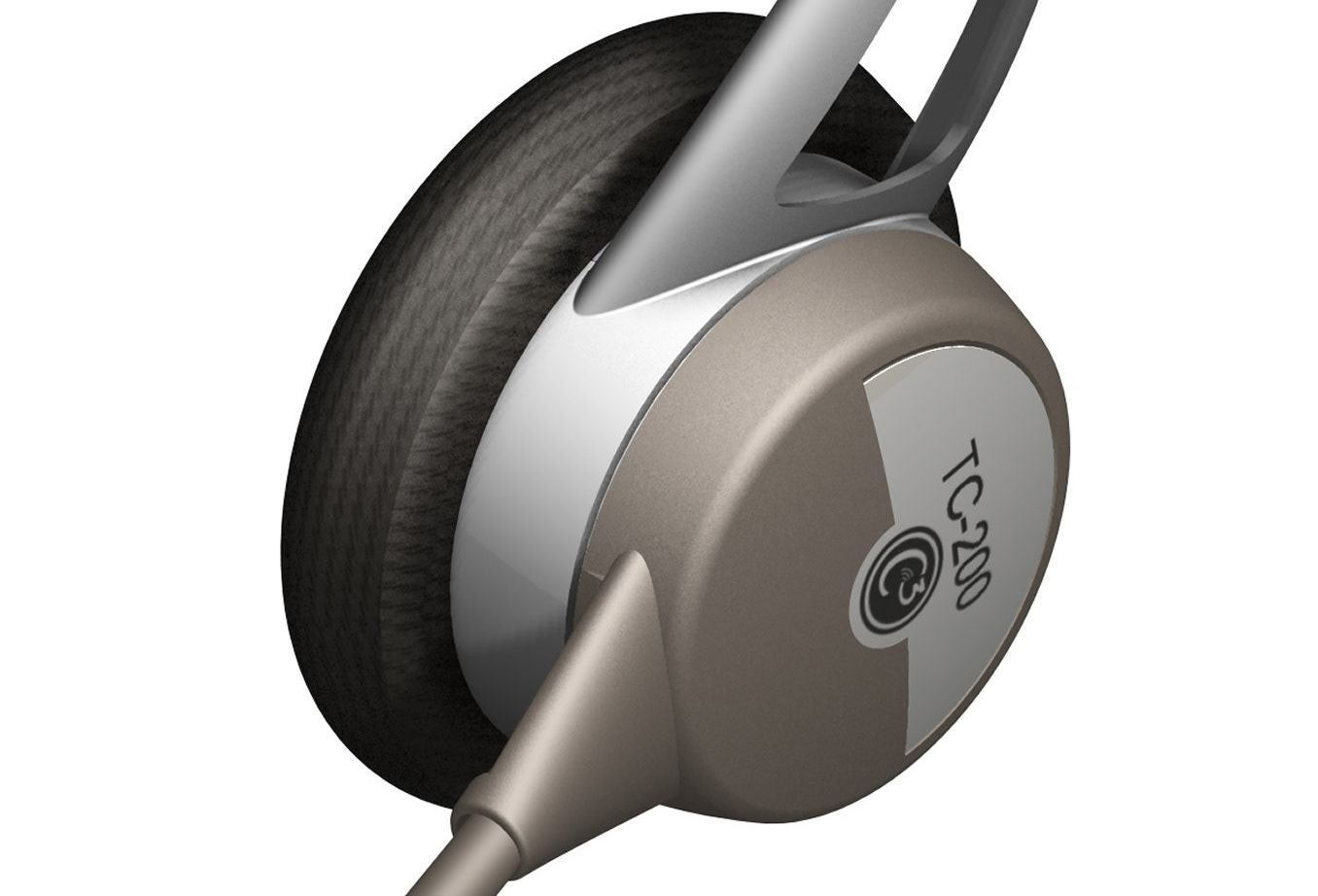
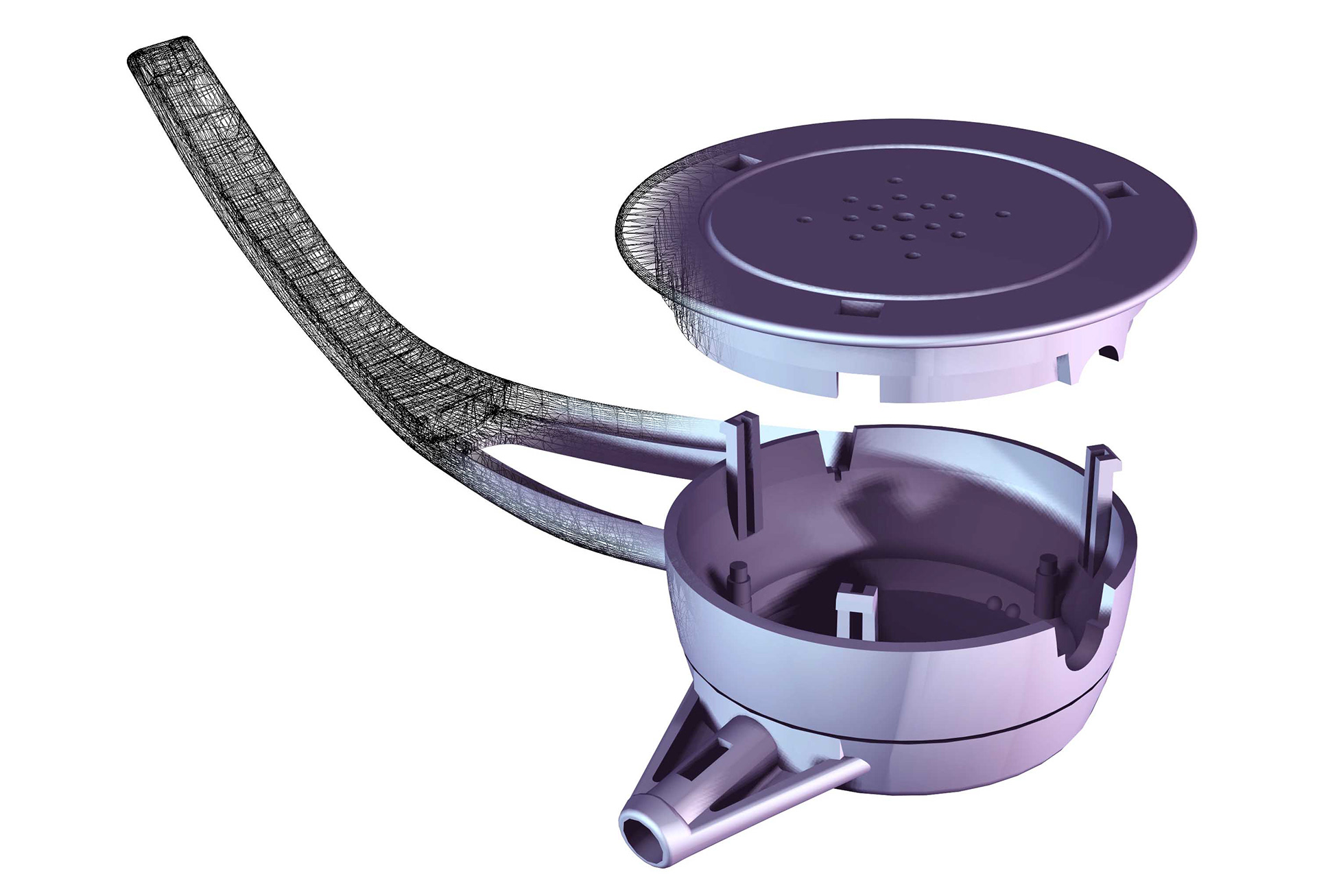
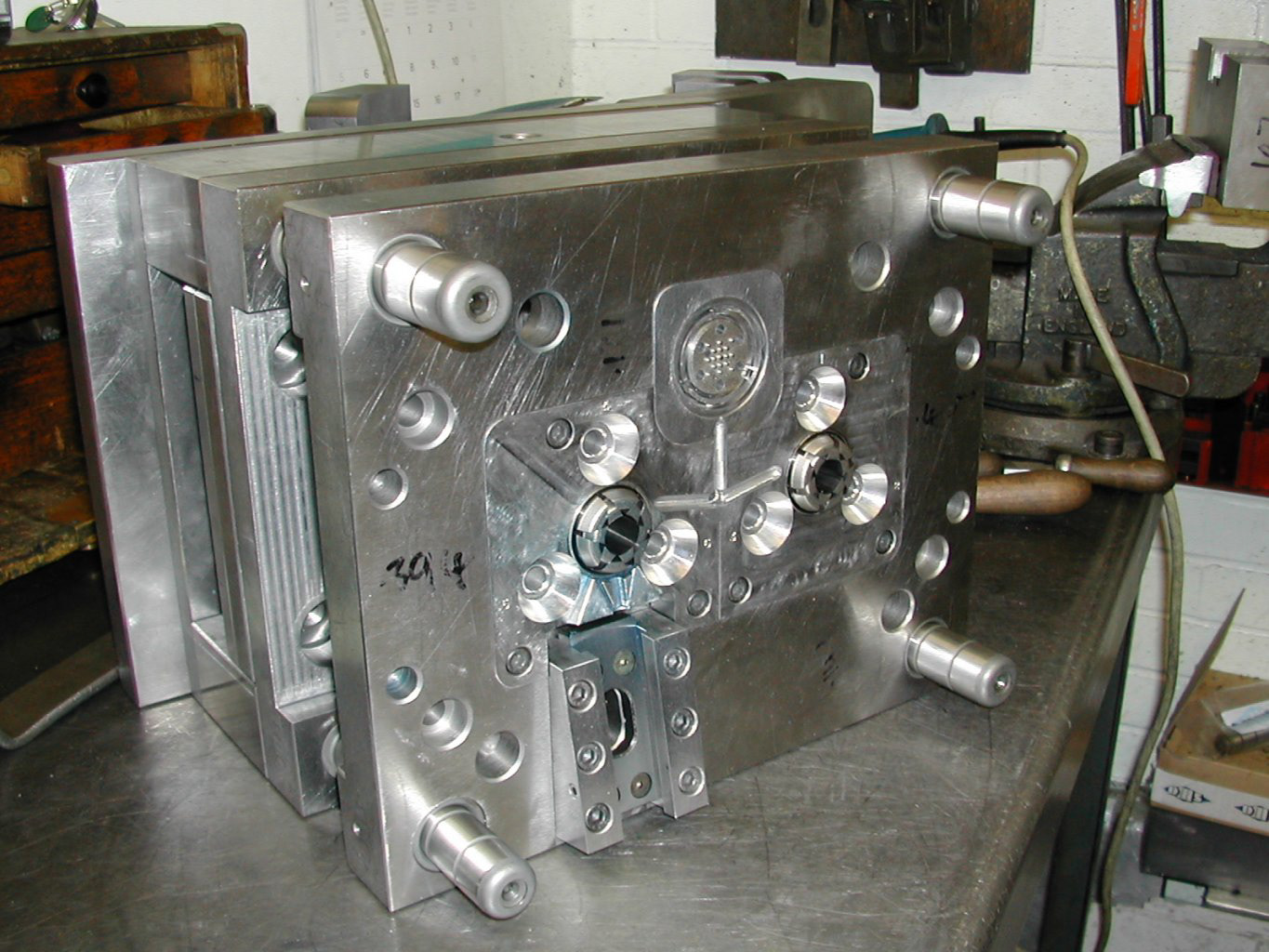
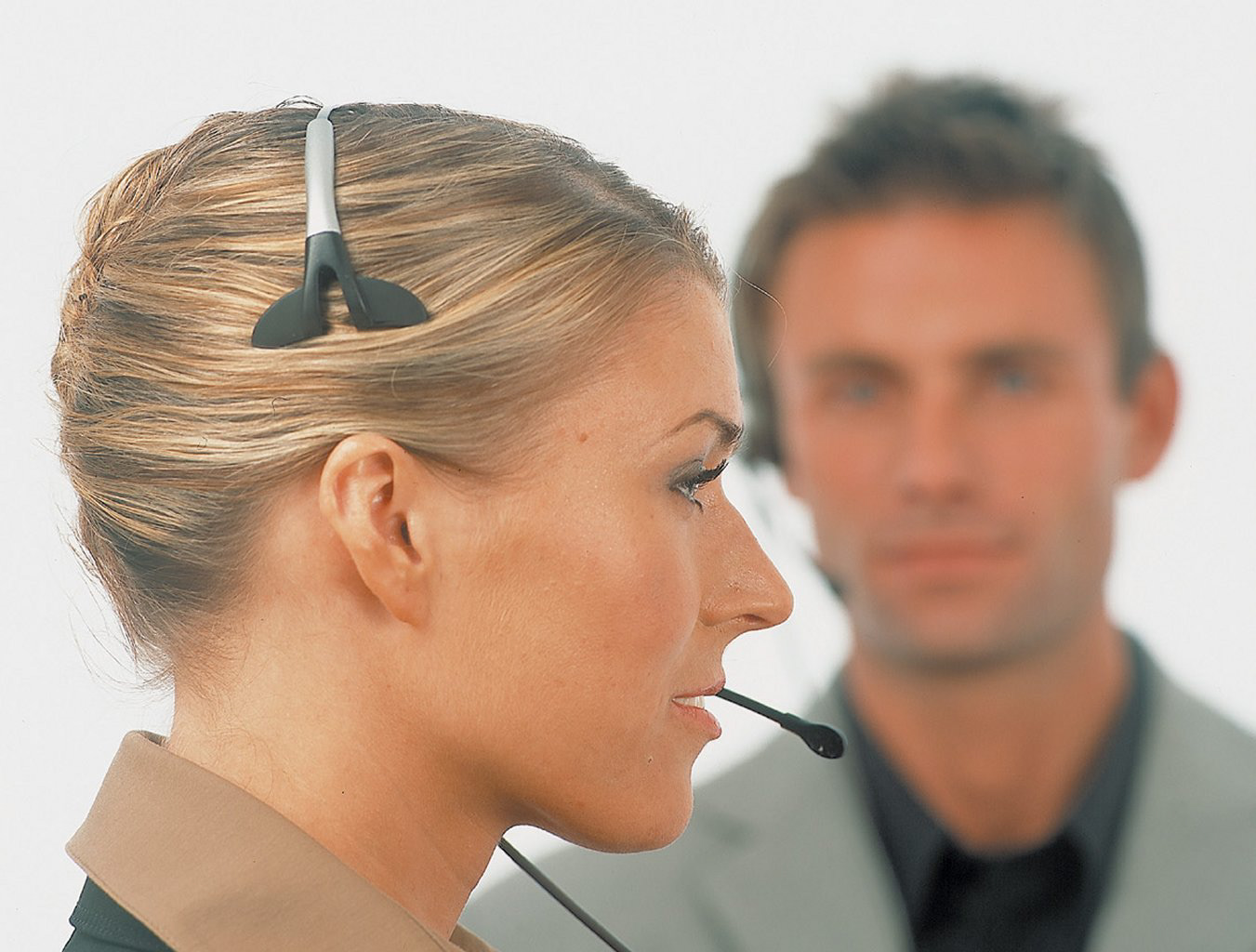
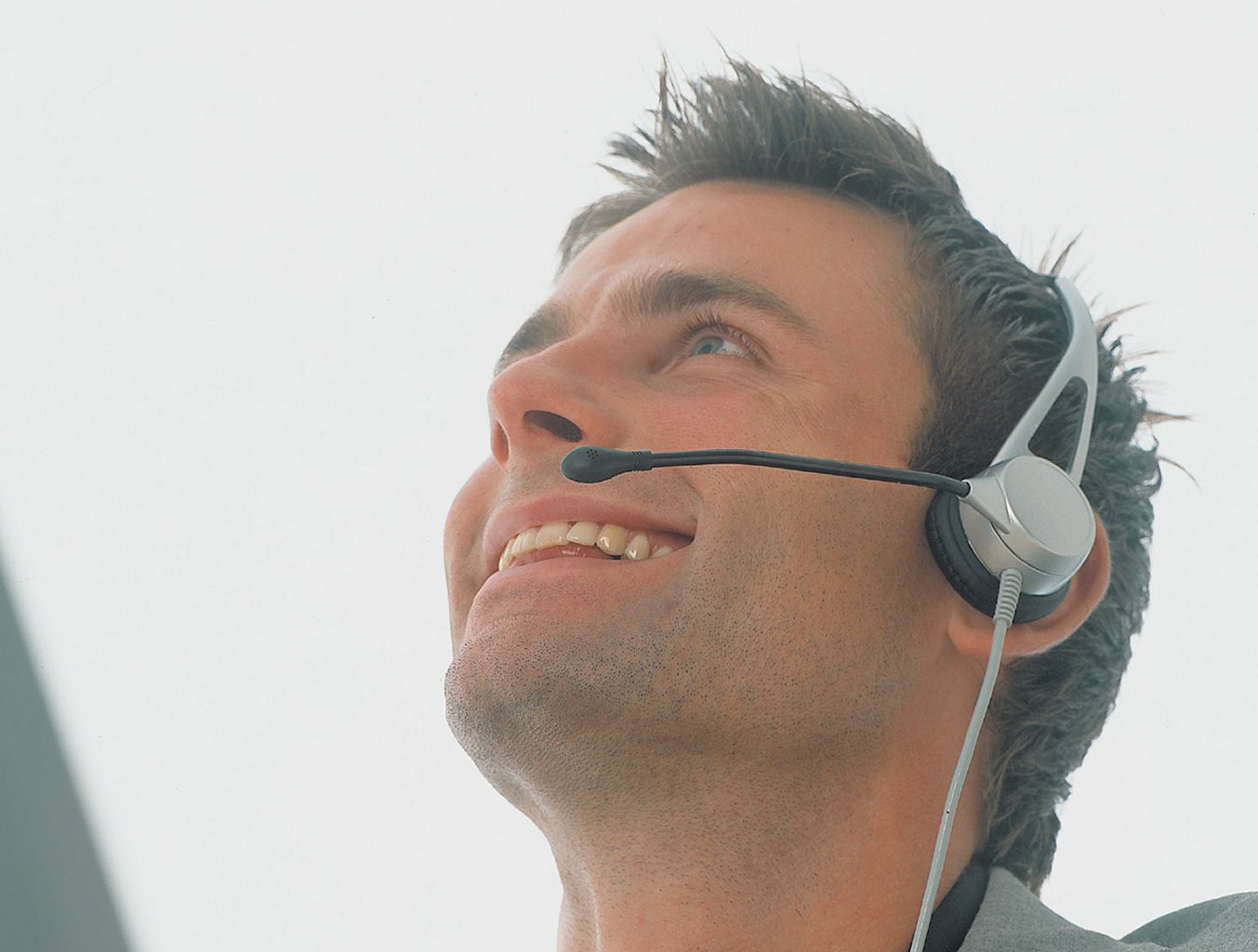
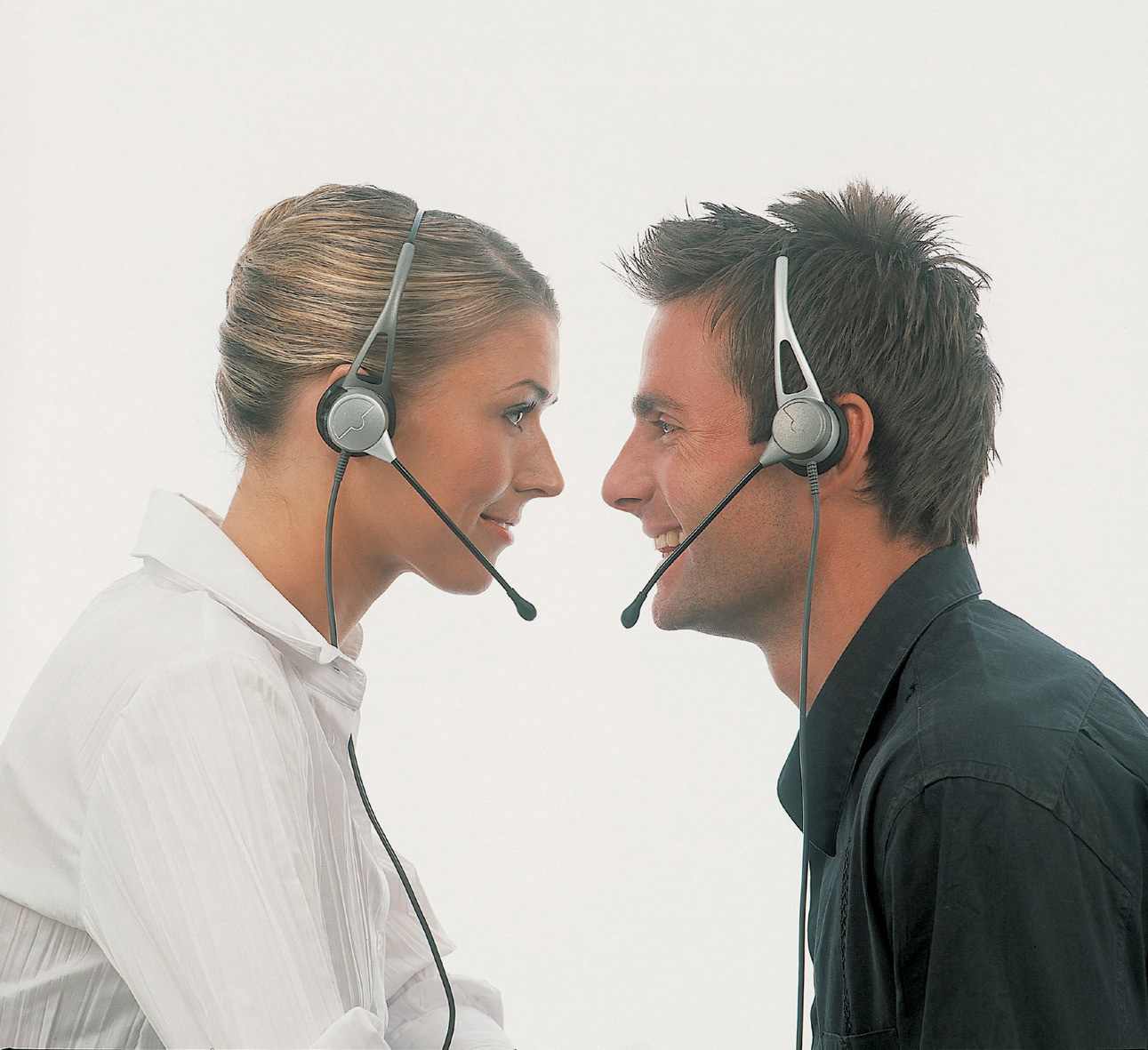
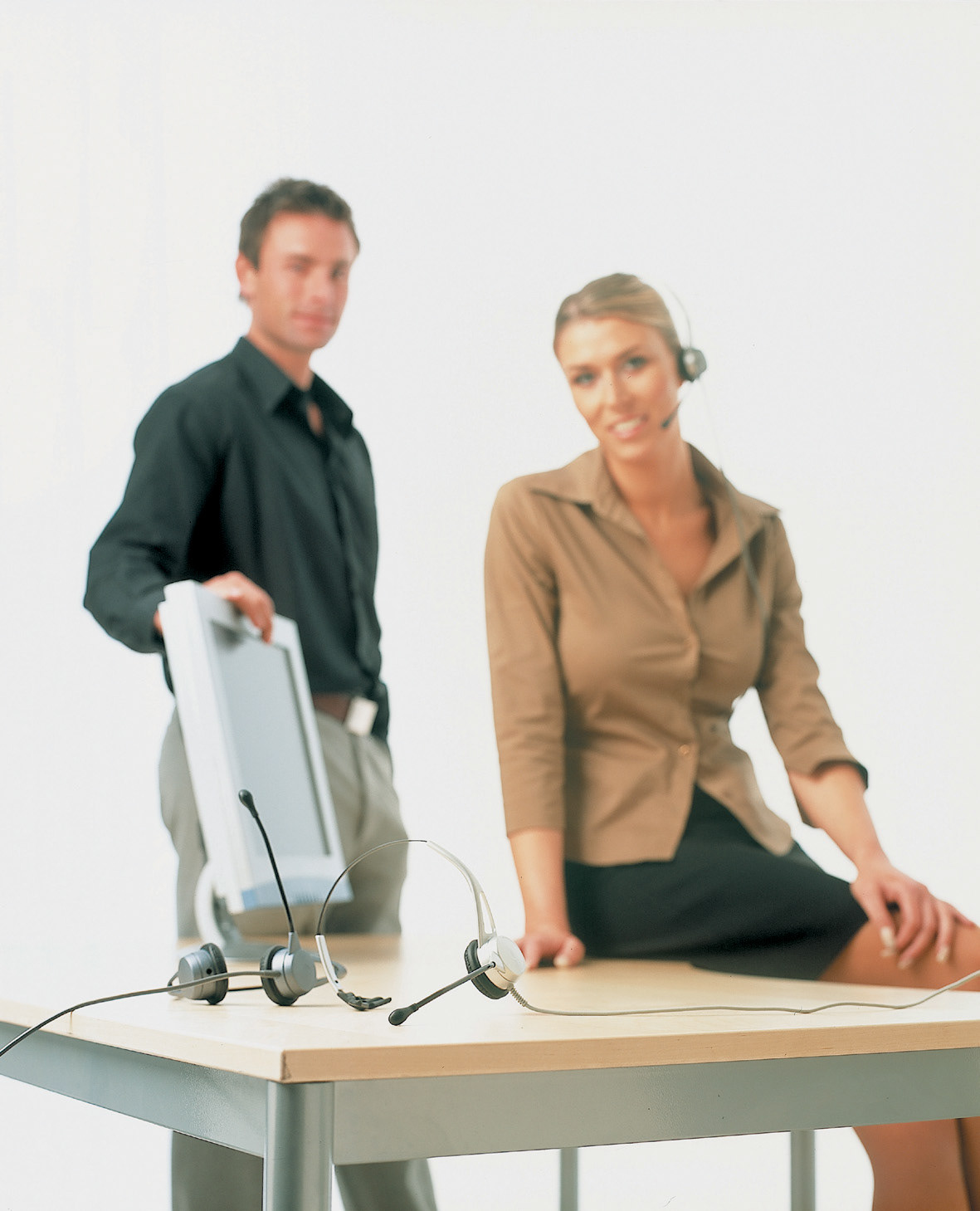
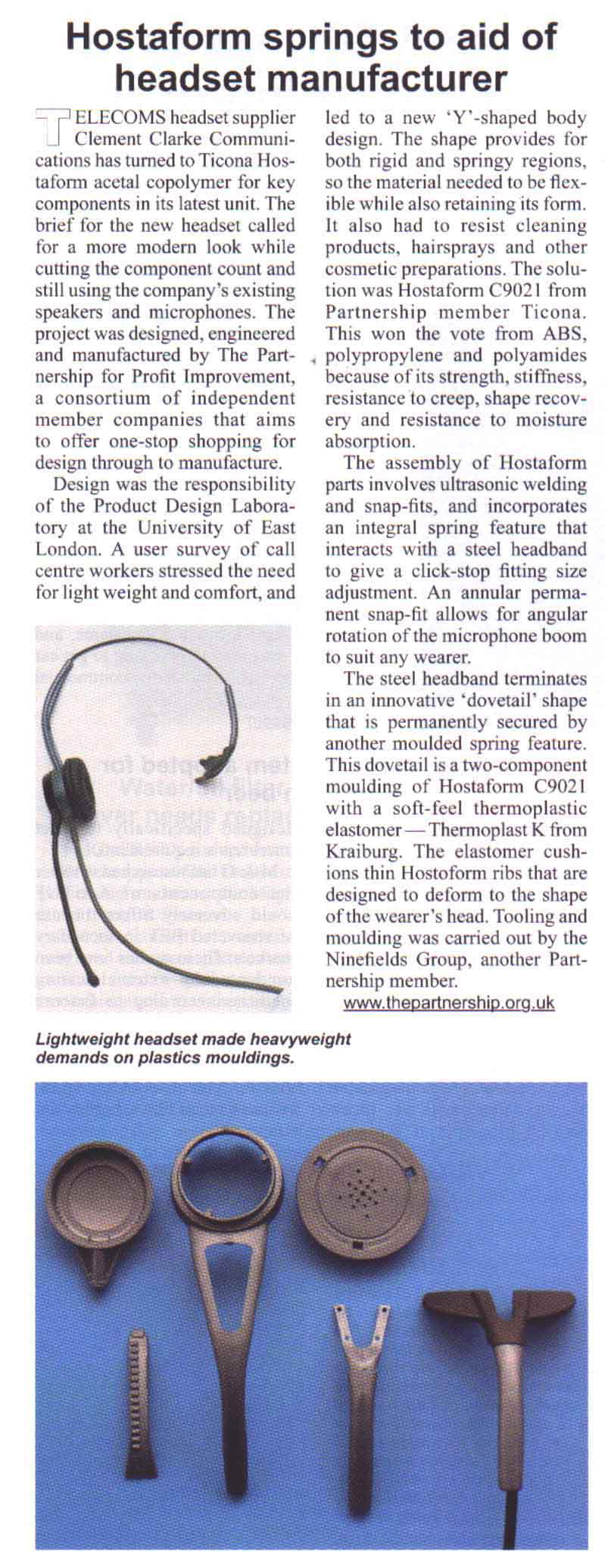